5 Signs Your Industrial Concrete Coating Needs to Be Repaired or Replaced
September 27th, 2024
5 min read
By Tom Dassie
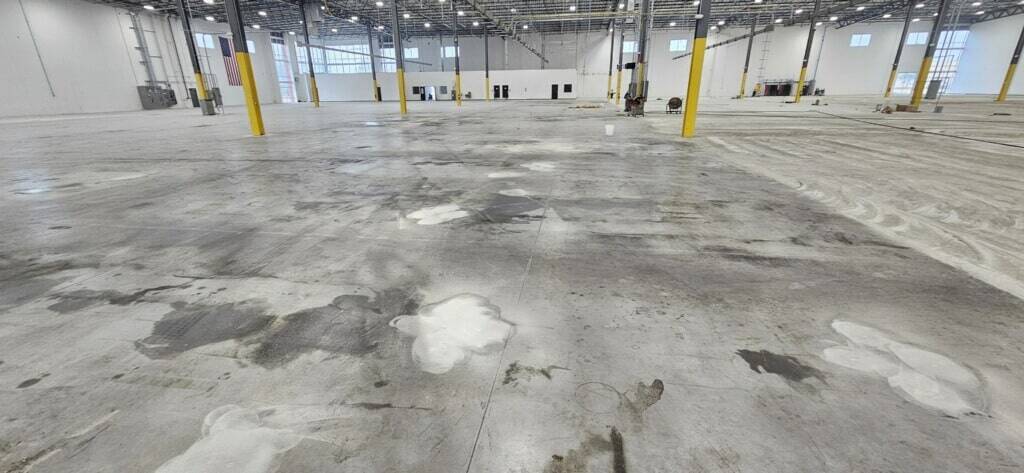
Concrete coatings in industrial settings are critical to maintaining a safe and efficient work environment. With heavy machinery like forklifts, constant foot traffic, and the frequent movement of goods, your flooring takes a beating every day.
Maybe you have a polished concrete floor, maybe you opted for a textured sealed epoxy, or a urethane cement solution. No matter what kind of coated concrete flooring you have, when the concrete coating starts to deteriorate, it can have ripple effects throughout your operations… damaging equipment, creating safety hazards, and ultimately leading to costly repairs if left unaddressed.
So, how do you know when it’s time to repair or replace your concrete coating? We at CustomCrete have been doing this for 20 years, we have seen it all, and we know what to look for. Let’s explore five warning signs that may indicate your warehouse floor might need attention before things get worse.
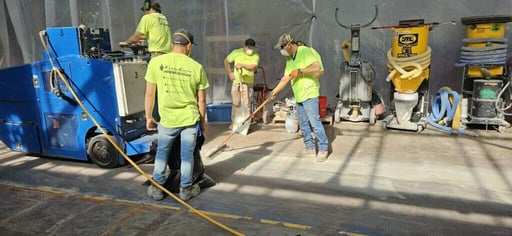
1. Forklift Damage, Trip Hazards, and Spills from Skids
In a busy warehouse, forklifts are essential for moving heavy loads across the facility. But maybe you have noticed that your forklifts seem to be taking more damage than usual? Or maybe you've spotted boxes slipping off skids during transport. Forklifts have no suspension, and on a bumpy floor your forklift drivers will start to experience back pain. These issues could be signs that your concrete coating is no longer up to the task.
An uneven, worn, or damaged floor can cause forklifts to jostle, leading to potential damage to the machinery itself or, worse, accidents involving loads tipping or falling over. Similarly, trip hazards can emerge as coatings wear down, putting your workers at risk.
These problems often occur when the coating loses its smooth, even surface. Bumps, cracks, or pits then interfere with equipment operation. Addressing these issues quickly can prevent more serious damage to your facility, keep your workers safe, and avert really costly liability issues down the line.
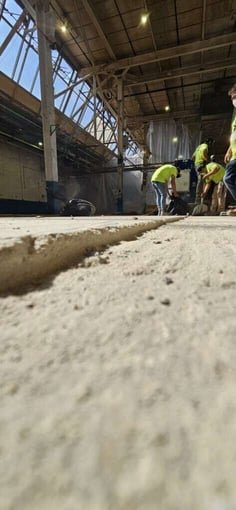
2. Delamination: When Your Coating Starts to Peel Away
Delamination is a major red flag that your concrete coating is failing. This happens when the bond between the concrete surface and the coating weakens, causing sections of the coating to peel, bubble, or flake away. In a warehouse, this is a serious issue. It creates an uneven floor and exposes the concrete to moisture and impact.
Delamination is often caused by improper surface preparation before the coating was applied or by moisture seeping into the concrete. If you notice areas where the coating appears to be lifting, bubbling, or separating, it’s time to act. Reapplying a coating over delaminated areas without fixing the underlying problem will only lead to more costly repairs down the line.
In extreme cases, large areas of delaminated coating may need complete removal and replacement. This will ensure the new coating bonds properly to the surface.
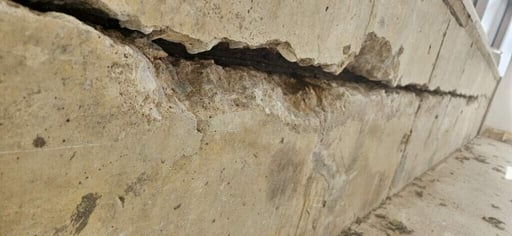
3. Concrete Cracking: A Sign of Structural Stress
Cracks in your concrete coating are another clear indicator that repairs or replacement may be needed. In a busy warehouse, cracks can form in the floor. Forklifts, heavy equipment, and the settling of the building and concrete slab cause constant stress.
Small hairline cracks might seem like a minor cosmetic issue, but they can quickly grow into larger cracks that compromise the structural integrity of the floor. A crack creates a path for moisture, oils, and chemicals to seep into the concrete. This causes more damage beneath the surface. This can eventually lead to pitting, fissure, or more serious issues that will require extensive repairs.
Regular inspections between seasonal temperature swings can help you catch cracks early before they escalate. Repairs may involve sealing small cracks, depending on severity. Larger, widespread cracks may require resurfacing the area. No matter your situation, experience tells us it is always less expensive to do it right the first time.
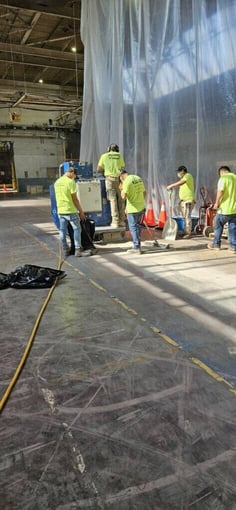
4. Persistent Dusting: A Sign of Coating Breakdown
Have you noticed an unusual amount of dust accumulating in your warehouse, even after regular cleaning? This could be a sign that the protective layer of your concrete coating is breaking down, a phenomenon known as dusting.
Dusting occurs when the top layer of the concrete coating erodes, releasing fine particles of concrete into the air and onto your floors. Not only does this make the warehouse harder to keep clean, but it also signals that the floor’s surface is degrading and needs attention. Over time, dusting can worsen, leading to more serious damage like cracks, holes, or uneven surfaces.
A new protective coating or a de-duster can help. It will extend your floor's life and keep your warehouse dust-free.
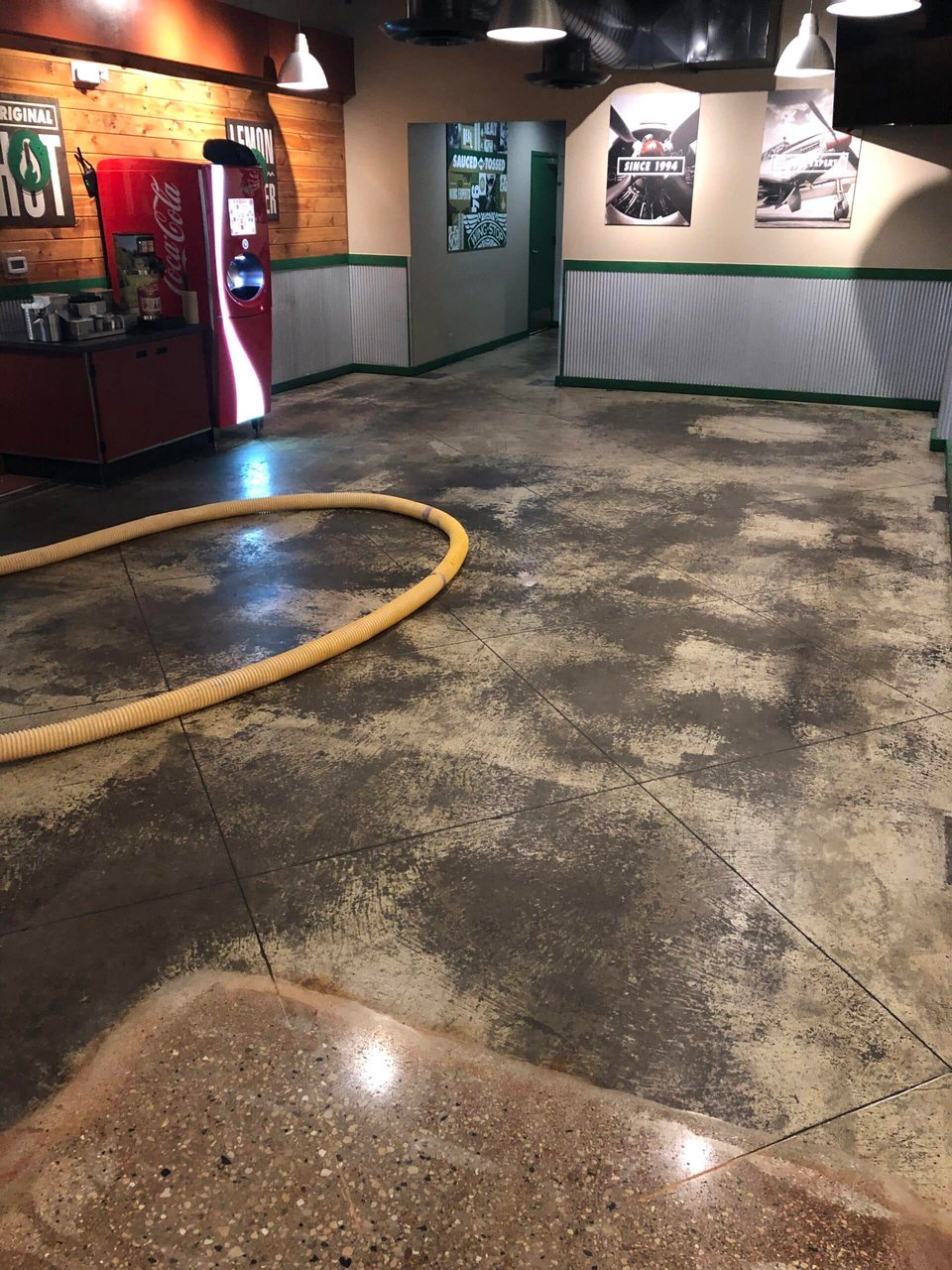
5. Staining and Chemical Damage: A Warning Sign for Warehouse Floors
Stains are more than just a cosmetic problem in warehouse settings. If you notice widespread staining, especially from chemicals, oils, or other corrosive materials, it could indicate that the protective coating on your floor is no longer doing its job.
When a concrete coating is functioning properly, it creates a barrier that prevents liquids from seeping into the porous concrete beneath. But, over time, harsh chemicals or heavy traffic can degrade this protective layer. It can lead to stains that are hard, or impossible, to remove. Worse, chemicals can seep into the concrete. They can weaken it, causing serious damage like pitting or cracking.
In some cases, deep stains may be a sign that moisture or chemicals are penetrating the floor, causing long-term damage. This is especially important in warehouses where spills are common. When cleaning no longer removes stains, it’s a sign that your coating needs to be replaced to prevent further deterioration.
Repair and Replacement Options
1. Resurfacing and Resealing for Widespread Damage
If your floor is showing early signs of wear, such as moderate cracking, delamination, or rough patches, resurfacing may be the best solution. This process involves grinding down the damaged top layer and applying a fresh layer of concrete sealer or epoxy. Resurfacing helps improve the appearance of the floor while extending its lifespan, preventing further damage from traffic or environmental factors.
Resealing is a flexible option that can be tailored to your warehouse's specific needs. Choosing the right materials will protect your floor. It will withstand heavy machinery, foot traffic, and chemicals. This will keep it durable and avoid a full replacement.
2. Addressing Large-Scale Wear with Resurfacing and Recoating
For floors with heavy wear, like large areas of peeling or abrasion, resurfacing and recoating may be best. This process involves grinding down the damaged areas and applying a new layer of sealer or epoxy, which restores both the function and appearance of the floor. This solution works well when the underlying concrete is still in good condition, but the coating has deteriorated.
Resurfacing protects against future wear and tear. It lowers the risk of damage from forklifts, spills, and daily use.
3. Full Replacement for Severely Damaged Floors
When a floor suffers from deep cracks, severe delamination, or large-scale pitting, a full replacement may be the only viable solution. This process involves removing the damaged coating entirely and replacing it with a new, durable layer. Full replacement is often necessary when the structural integrity of the concrete has been compromised or when resurfacing is no longer an option.
This process can be more involved. But, it often works best. It ensures long-term durability and safety in high-traffic warehouses.
4. Specialized Coatings for Heavy-Duty Environments
Some industries may require specialized coatings for tougher conditions. Coatings like urethane cement are designed for environments where temperature fluctuations, heavy machinery, or chemical exposure are common. These coatings offer superior durability and are better suited for handling the wear and tear of industrial spaces.
Choosing the right coating for your warehouse protects the floor. It reduces the need for frequent repairs or replacements.
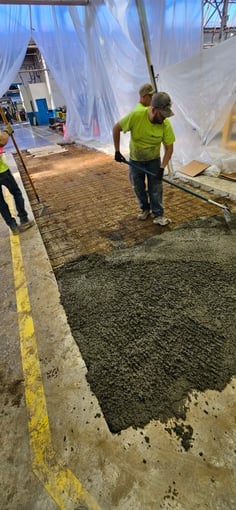
Why Timely Repairs Matter for Concrete Coatings
Ignoring signs of a failing concrete coating can be risky. It can damage equipment and lead to costly repairs. Cracks, pitting, delamination, and moisture issues can worsen. A minor repair can become a full replacement. In an industrial setting, where safety and efficiency are critical, keeping your floor in top condition should be a priority.
At CustomCrete, we diagnose concrete floor issues. We then provide custom repair or replacement solutions for industrial and commercial settings. Don’t wait for the problems to get worse.