How Much Does Polished Concrete Really Cost? Breaking Down the Price Per Sq Ft
September 10th, 2024
5 min read
By Tom Dassie
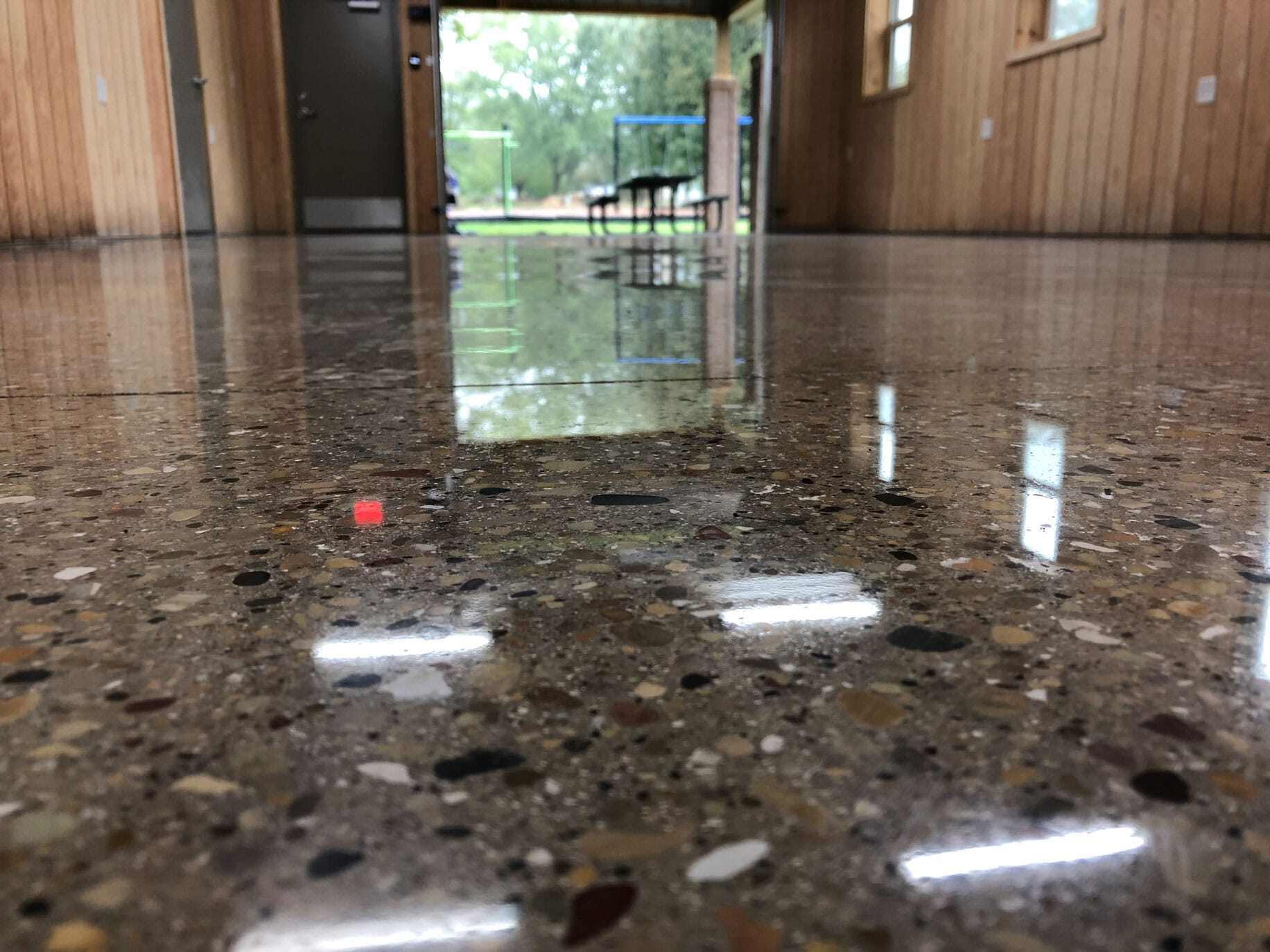
If you're trying to figure out how much polished concrete will cost for an industrial flooring project, you’re likely feeling overwhelmed. Between the different levels of gloss, surface preparation, patching, and other factors, it can be hard to get a clear idea of what you’ll end up paying. Plus, the condition of your concrete slab directly determines the outcome, so it can be tough to even have a good idea of what the outcome will look like. Whether you’re working on a warehouse floor or a showroom, finding an accurate price and having realistic expectations of outcomes is crucial for planning your project and your budget.
We understand how frustrating it is to navigate the planning stages without clear information. Many of our customers have been in the same position as you are. Unsure of what’s reasonable or what to expect. At CustomCrete, we’ve seen it all firsthand, and we’re here to help you have all the information you need going in.
With over a decade of experience handling polished concrete projects, we’ve honed the process of providing accurate and transparent cost breakdowns. In this guide, we’ll explain what you can expect to pay per square foot and how factors like surface prep, finish type, and project complexity influence the final price. We will also give you some idea of what to expect in the final look of your project.
As a disclaimer: Every job is different. This article assumes a standard project using basic parameters. It should provide a rough estimate for projects, not a guaranteed quote.
How Much Does Polished Concrete Cost Per Square Foot?
For a 5,000-square-foot project, polished concrete generally costs between $3 and $6 per square foot. This means you can expect to pay anywhere from $15,000 to $30,000, depending on the level of gloss, the condition of the surface, and the complexity of the job.
Note: Larger projects bring the cost per square foot down substantially, so a 100,000 square foot project might cost half per square foot as a job like our example.
But what does that range really mean for your project? Let’s break down the key factors that influence these costs.
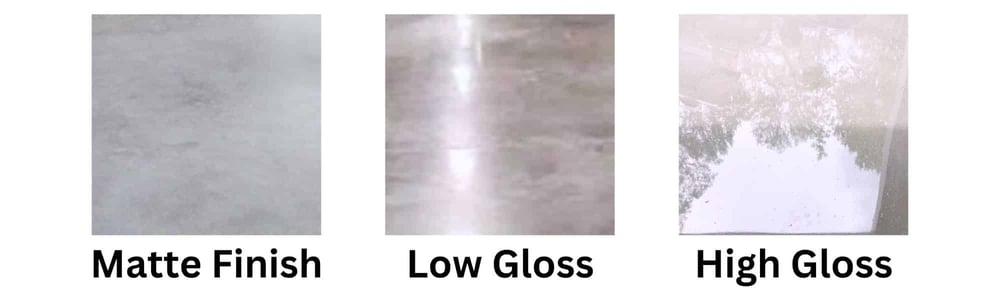
Types of Polished Concrete Finishes and How They Impact Costs
The type of finish you choose has a significant impact on the overall cost of your polished concrete project. Basically, you are deciding just how shiny and glossy you want your concrete floor to be.
A matte finish, achieved using 50 or 100 diamond grit, is ideal for spaces that don’t require a high-gloss look, such as industrial warehouses or functional areas. This finish is typically more affordable due to the reduced amount of grinding and polishing required.
A low gloss finish uses 200 or 400 diamond grit and offers a subtle shine, making it a popular choice for commercial spaces that want a more refined appearance without the high sheen of a glossy surface. The additional polishing needed for this finish increases the cost compared to a matte option.
A high gloss finish, using 800, 1500, or even 3000 diamond grit, you’ll achieve a neer mirror-like surface. This is a popular choice for showrooms or upscale retail spaces where aesthetics are a priority. However, the labor-intensive polishing process required for this finish puts it at the higher end of the pricing scale.
All of these options are highly durable, easy to maintain, resistant to moisture, and long lasting options, you are really just selecting for how glossy you want the finished product to be.
Factors That Influence Polished Concrete Pricing
While the type of finish plays a major role in determining the cost, there are additional factors that can influence your final price.
Size of the Area
Area size matters because larger projects tend to lower the cost per square foot due to greater labor efficiency. Contrastly, smaller areas can increase the cost per square foot, as fixed expenses like mobilization and cleanup must be factored in across a smaller surface.
Condition of the concrete
If your concrete is in good shape, minimal repair work is needed, keeping the price on the lower end of the scale. However, if the floor has cracks, old coatings, or adhesives from carpeting or vinyl or whatever else, that need to be removed, and additional surface preparation like deeper grinding or patching will be required. This can drive up both time and labor costs.
Complexity of the space
The complexity of the space also plays a role. A large, open area such as a warehouse allows for more efficient work, reducing labor time and costs. However, spaces with affixed machinery, cubicles, kennels, vats, or tight corners require more time and effort to work around, increasing labor expenses.
Accessibility
Accessibility to the job site can impact pricing. Projects that are easily accessible, with features like a loading dock or ramp, allow for quick transport of heavy equipment and materials, keeping costs down. On the other hand, if the project is located on a higher floor with limited elevator access, more labor and time will be required, increasing the overall cost.
Dust Removal
The grinding process required to prep the surface of your polished concrete produces a large amount of fine but very heavy stone dust. Proper disposal is imperative, and thus it is a cost to expect.
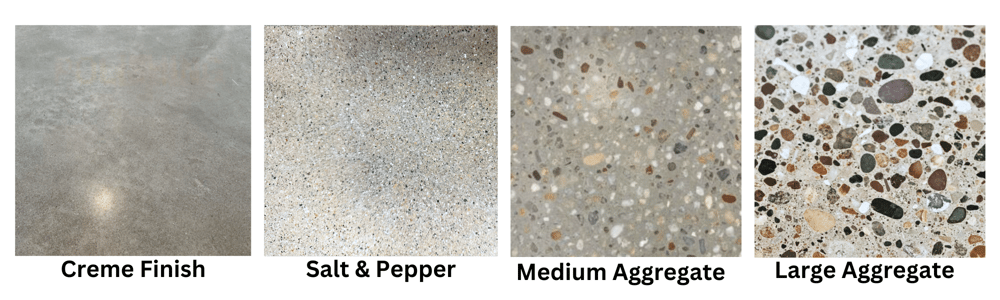
How the Condition of Your Concrete Affects the Final Look
Cream Finish
A cream finish offers the smoothest and most uniform look, with little to no aggregate exposure. This is achieved through minimal grinding, which preserves the top layer of the concrete. The result is a sleek surface with a consistent color and texture, ideal for spaces where a refined, high-gloss appearance is desired. However, it’s important to note that since this finish doesn’t remove imperfections or blemishes in the concrete, any existing surface defects may still be visible. Note: this is not possible for all floors.
Salt and Pepper Finish
A salt and pepper finish exposes fine aggregate, giving the surface a slightly textured look. This finish requires more grinding than a cream finish but is still relatively light. It’s a popular choice for commercial and residential spaces, offering a balance between aesthetic appeal and slip resistance. The texture comes from the small particles of sand and fine aggregate that are revealed during the polishing process. This option is often used for spaces where a subtle, decorative look is needed without the roughness of larger aggregates.
Medium Aggregate Exposure
For those looking for more texture and character in their concrete, a medium aggregate exposure reveals larger aggregate particles within the slab. This finish involves more aggressive grinding to expose a significant portion of the stone embedded in the concrete. It creates a striking, rugged surface. At home in industrial settings where slip resistance and durability matter.
Large Aggregate Exposure
A large aggregate exposure involves the most aggressive grinding, revealing the largest stones and aggregate embedded in the concrete slab. This finish is ideal for spaces that prioritize durability and slip resistance, such as warehouses or heavy-traffic areas. The exposed aggregate provides a rugged, highly textured surface that’s perfect for environments requiring maximum strength and a unique, terrazzo-like aesthetic. This option is typically more labor-intensive and costly due to the deep grinding required.
Ready for a quote?
When it comes to polished concrete, knowing the range of costs and the factors that can influence pricing helps you make an informed decision. From the finish type to the condition of your concrete, each element plays a part in determining the final price. Larger projects often bring down the cost per square foot, while smaller, more complex spaces may increase it. By considering factors like surface preparation, accessibility, and the desired finish, you can better plan for your project. No matter your choice, polished concrete is a durable, long-lasting solution. It enhances any industrial or commercial space.
If you’re ready to get a precise quote for your project, the next step is simple: Contact us for a quote. We’ll walk you through the options and make sure you get exactly what you need, without any surprises.
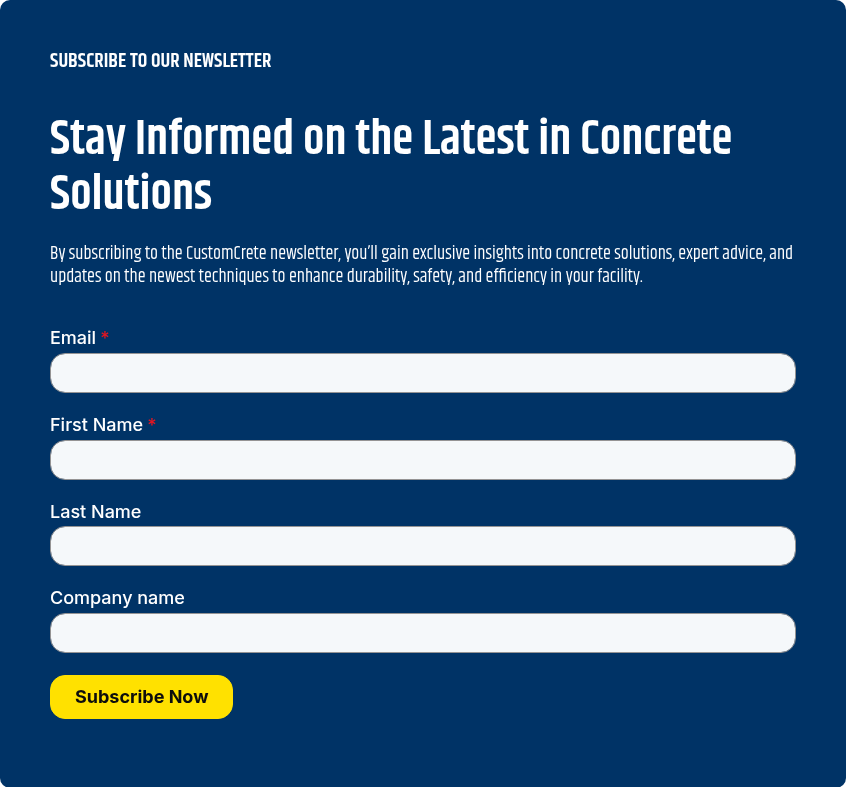