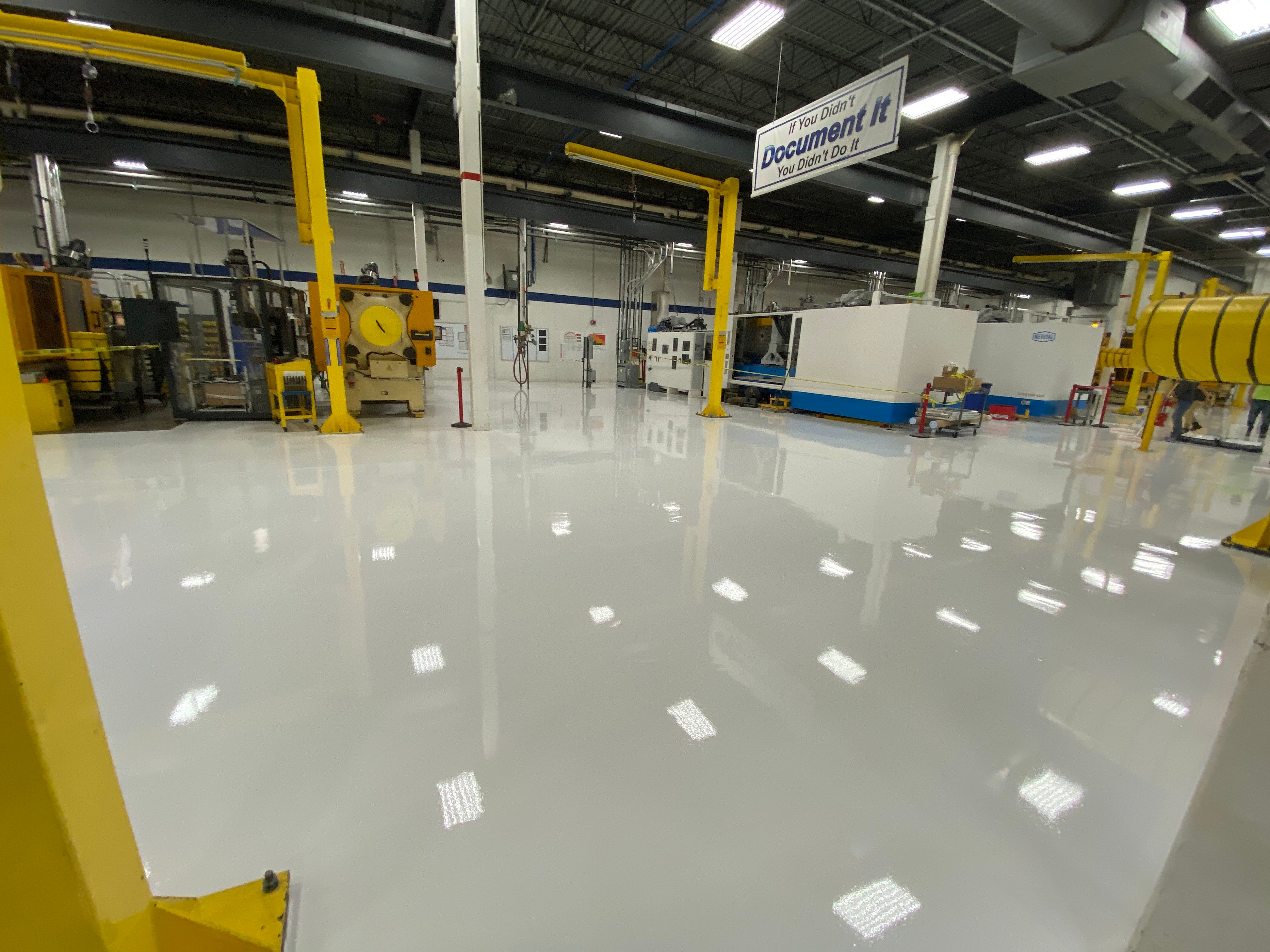
Epoxy floors are a popular choice for their durability, strength, and good looks. People often choose epoxy because it offers a long-lasting and visually appealing solution for both industrial and commercial settings. However, epoxy floors are not perfect. Sometimes, they can come with unexpected problems that cause frustration and lead to extra expenses down the road if not addressed correctly.
We know how disappointing it can be when an epoxy floor does not meet expectations. You invest time and money expecting it to perform well, but when issues start popping up early, it can feel like a letdown. The good news is that most of these frustrations can be avoided with the right information and a bit of proactive effort. We understand the need for peace of mind when it comes to your flooring, and we want to help you get there.
This article will walk you through the seven most common problems with epoxy floors and how to avoid them. Knowing what to expect and taking the proper steps can ensure you get the performance and longevity you paid for. Let’s dig in and make sure your epoxy floor does not end up becoming a problem.
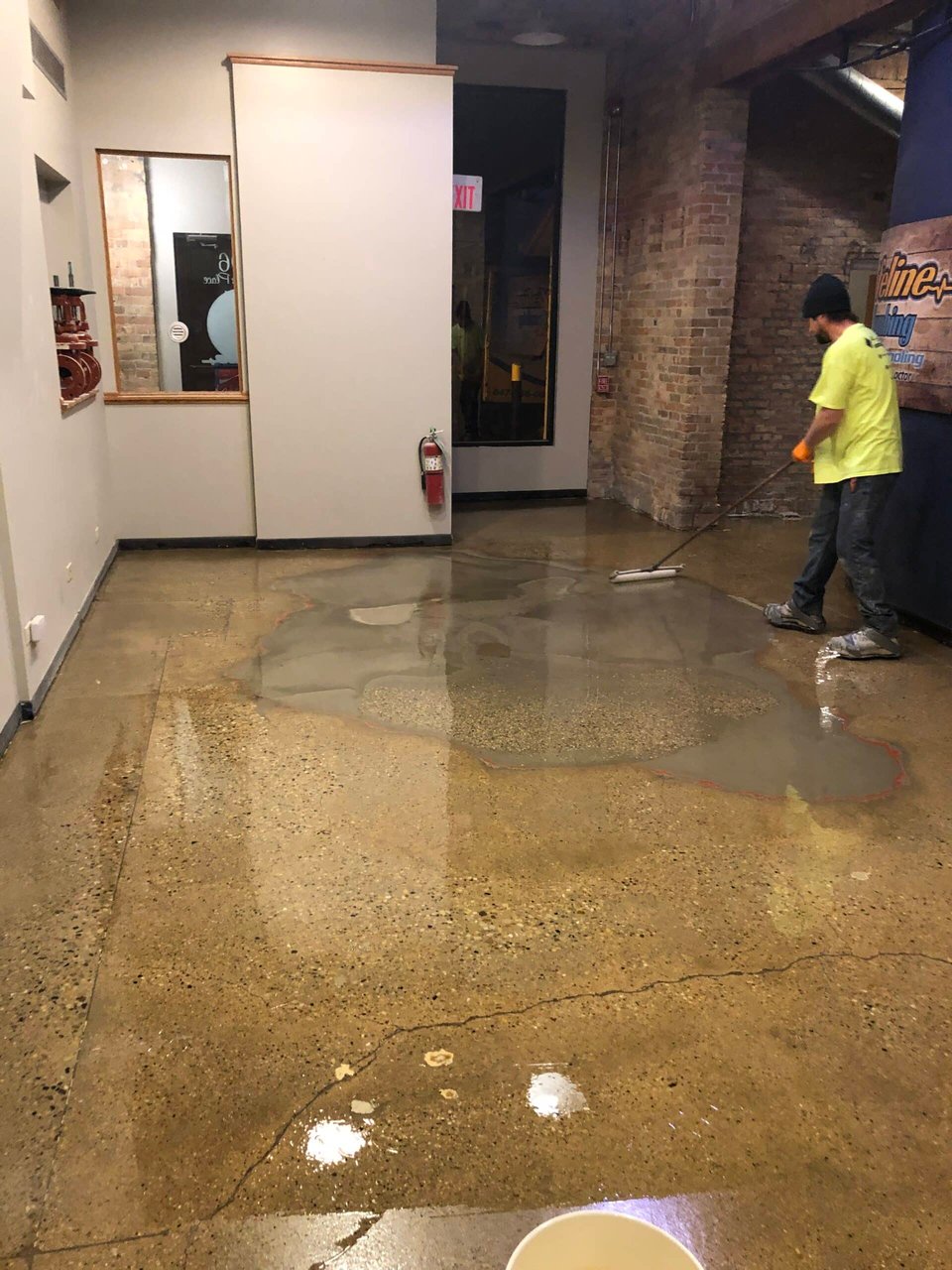
Problem #1: Improper Surface Preparation
What It Is:
One of the biggest reasons epoxy floors fail is poor surface preparation. This can happen if the surface is not cleaned properly, has dust or debris, or if moisture is trapped within the concrete. When the surface is not prepped correctly, the epoxy cannot adhere properly. This leads to issues like bubbles, peeling, or delamination, where the epoxy lifts from the concrete and starts coming apart.
How to Avoid:
The key to a successful epoxy floor is thorough preparation. It starts with grinding, shot-blasting, or scarifying the concrete surface to open up the pores and create a texture that the epoxy can bond to. This is known as mechanical preparation, and it is essential for getting the best results. Next, the surface must be thoroughly cleaned. All dust, grease, oil, and debris need to be removed to create a clean canvas for the epoxy to bond with.
Problem #2: Outgassing and Fisheyes
What It Is:
Trapped air during application is a common problem with epoxy floors. When air gets trapped beneath the epoxy, it forms bubbles as the coating cures. These bubbles can be unsightly and weaken the floor, leading to further issues down the line.
How to Avoid:
Applying the epoxy in thin layers is one of the most effective ways to reduce air bubbles. Thin layers allow the air to escape as the epoxy settles. It is also important to ensure that the surface is properly primed. A primer helps seal the concrete and minimize the chance of air escaping from the substrate into the epoxy layer. Using a spiked roller during application can also help release trapped air and flatten out any bubbles that might form. This step ensures a smooth, even finish that looks good and holds up over time.
Problem #3: Discoloration from UV Exposure
What It Is:
Epoxy is strong, but it is sensitive to sunlight. When exposed to UV rays, epoxy floors can start to yellow or discolor over time. This can be a major issue, especially for areas where sunlight is unavoidable. The discoloration not only affects the appearance of the floor but can also weaken the coating, making it less effective.
How to Avoid:
If your epoxy floor will be exposed to sunlight, it is important to use a UV-resistant topcoat. Polyurethane and polyaspartic coatings are a good option because they provide an additional layer of protection and help prevent the epoxy from discoloring. Urethane is known for its resistance to UV rays and works well in both indoor and outdoor environments. Applying this type of sealer after the epoxy cures keeps the floor looking its best and adds another level of durability. It is a simple step that can make a big difference, especially for floors in high-visibility areas.
Problem #4: Moisture Vapor
What It Is:
Moisture vapor is a natural occurrence in concrete, and while it may not be noticeable, it can create significant problems for epoxy floors. As moisture moves up through the concrete, it can cause the epoxy coating to bubble, peel, or even delaminate over time. This issue is common in areas with high humidity or poor drainage, such as basements, warehouses, or outdoor spaces. Left untreated, it can compromise the durability of the epoxy and lead to expensive repairs.
How to Avoid:
The most effective way to prevent moisture vapor issues is by testing for it before applying the epoxy. Moisture testing methods such as surface-level meters, probe tests, or calcium chloride tests can reveal how much moisture is present in the concrete. If high moisture levels are detected, installing a moisture vapor barrier can safeguard the floor by creating a protective layer that prevents moisture from disrupting the epoxy.
In addition to moisture testing and barriers, maintaining proper drainage and ventilation in the area helps manage moisture levels.
Problem #5: Susceptibility to Scratches and Abrasions
What It Is:
While epoxy floors are durable, they are not immune to scratches, especially in areas with heavy machinery, foot traffic, or equipment movement. Over time, this wear and tear can cause the floor to lose its smooth appearance and look scuffed or damaged.
How to Avoid:
Applying a clear, durable topcoat over the epoxy adds an extra layer of protection. This topcoat can take the brunt of the wear, keeping the epoxy layer underneath intact. It is a simple way to extend the life of the floor and maintain its appearance.
Another preventative measure is implementing a regular maintenance routine. In high-traffic areas, consider using floor mats or protective pads under heavy equipment. This helps reduce direct contact with the epoxy surface and limits the potential for scratches. Regular inspections also help catch any signs of damage early, allowing for spot repairs before the issue spreads. This kind of proactive maintenance keeps the floor looking fresh and extends its lifespan. Proper forklift training and safety can also help to increase the lifespan of your floors coating.
Problem #6: Sensitivity to Temperature Fluctuations
What It Is:
Epoxy can crack or become brittle when exposed to extreme temperatures, especially if the environment fluctuates significantly between hot and cold. In industrial or commercial settings where temperatures vary, this can become a problem as the epoxy expands and contracts.
How to Avoid:
The best way to prevent this issue is to choose an epoxy formulation that matches the environment’s needs. Some epoxies are designed to be more flexible or resistant to temperature changes. For settings where temperatures fluctuate, select a temperature-resistant or flexible epoxy. This type of product is specifically formulated to withstand the stress of expansion and contraction without cracking.
Additionally, controlling the temperature during the installation process is important. Applying epoxy within the manufacturer’s recommended temperature range helps it cure properly and reduces the risk of future issues. If the environment is difficult to control, using fans, heaters, or other climate control methods can help create the right conditions for a successful installation.
Problem #7: Limited Lifespan Compared to Other Flooring Solutions
What It Is:
Epoxy floors are durable, but they do not last forever, especially in industrial settings with high levels of wear and tear. Compared to some other types of flooring, epoxy may have a shorter lifespan, particularly if it is not maintained properly or if the environment is harsh.
How to Avoid:
Regular inspections are key to catching signs of wear early. Spot repairs, topcoat reapplications, and fixing high-traffic areas can greatly extend an epoxy floor's life. They should be done before damage spreads. Implementing a maintenance plan that includes cleaning, touch-ups, and periodic reapplication of protective coatings helps the epoxy last longer.
If you are looking for a flooring solution that can handle even more wear and tear, consider alternatives like urethane cement. Urethane cement is known for its durability and ability to withstand extreme conditions, making it an ideal choice for areas where epoxy might not hold up as well. Understanding your environment and the demands placed on the floor can help you decide whether epoxy or an alternative solution is the best long-term option.
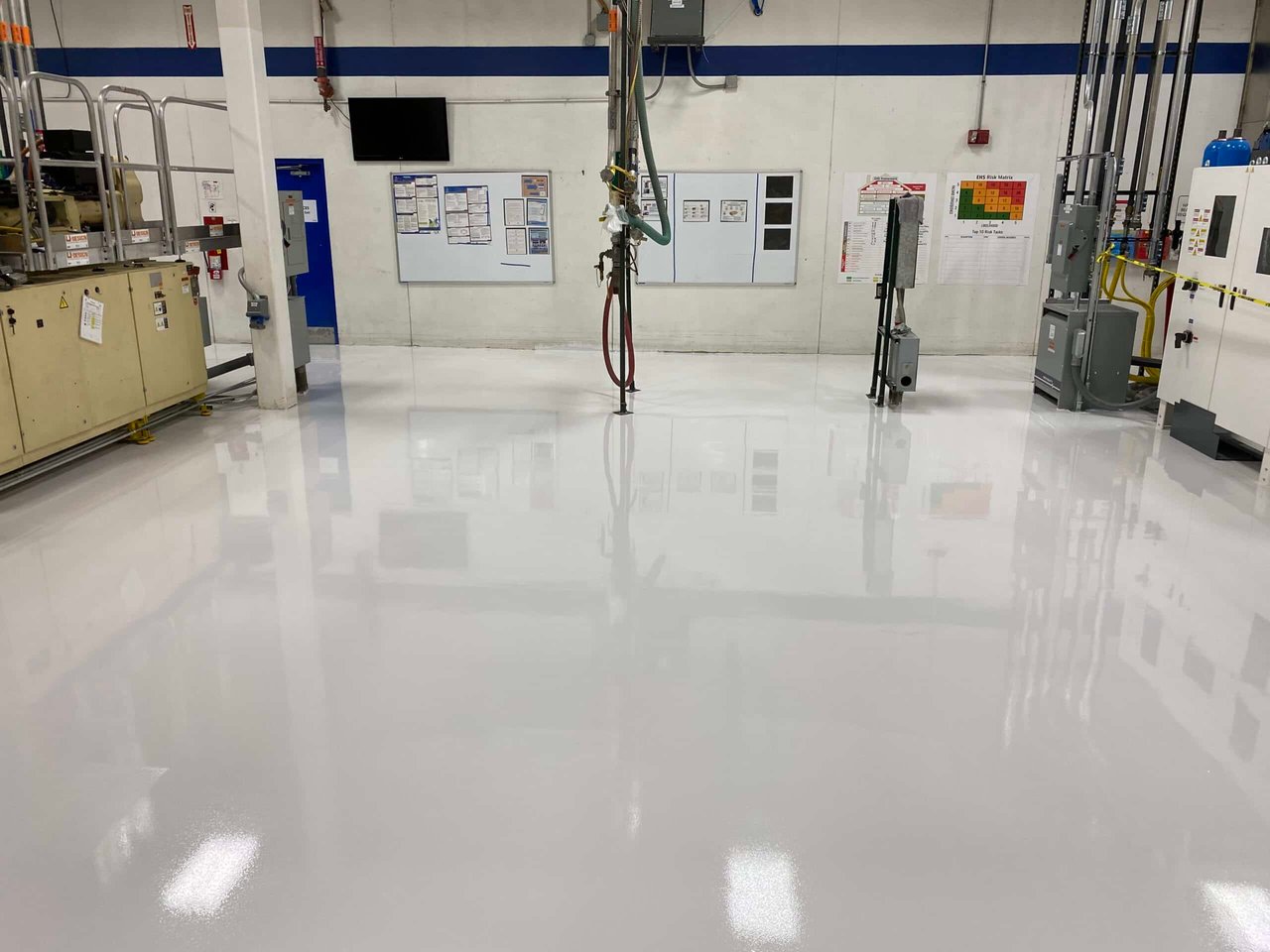
How to Get the Most Out of Your Epoxy Flooring
While epoxy floors have their challenges, understanding these issues and knowing how to prevent them can make a big difference. To keep your floor in top shape, take these steps: Prepare the surface. Use UV-resistant coatings. Add anti-slip additives. Choose the right epoxy for the environment.
A little maintenance and attention go a long way in keeping your floor safe, functional, and visually appealing for the long term. If you want to learn more about maintaining your epoxy floor or exploring other options like urethane cement, check out our resources on epoxy pricing. It is all about getting the most out of your investment.