Before and After Case: How a Bottling Facility Transformed Its Floors in Just Two Days
June 20th, 2025
2 min read
By Tom Dassie
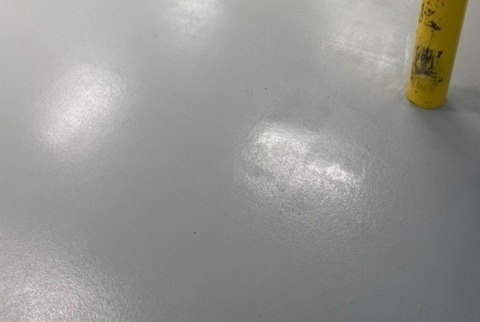
In fast-paced food and beverage facilities, the condition of the floors can’t be an afterthought. Surfaces need to be slip-resistant, seamless, easy to clean, and able to withstand daily wear from foot traffic, carts, and chemical cleaning.
When a local bottling company realized their existing floors were no longer meeting hygiene and safety expectations, they turned to CustomCrete for a fast, high-performance solution.
The Problem: Unsafe and Unsanitary Floors in a Bottling Facility
By early May 2025, this company’s hallway and production room floors had become visibly worn and inconsistent in texture. The lack of slip resistance, combined with cracks and porous areas, created safety hazards and made cleaning difficult. With production timelines to meet and no room for extended downtime, the facility needed a flooring upgrade—and they needed it fast.
The Solution: Sherwin-Williams Shop Floor Epoxy System
CustomCrete recommended the Sherwin-Williams Shop Floor System, a multilayer epoxy flooring solution engineered for industrial settings like food and beverage processing. This system was selected for its:
- Bacterial resistance to support sanitation goals
- Slip-resistant finish to improve worker safety
- Heavy-duty performance under regular traffic and cleaning
- Bright, uniform appearance to refresh the production space
Despite the scale of the job, the entire installation was completed in just two days: May 1–2, 2025.
What the Two-Day Process Looked Like
Installing a floor built for performance means every step matters. Here’s how the CustomCrete team executed this job from start to finish:
1. Diamond Grinding and Dust Control
To begin, the crew used diamond grinders connected to industrial HEPA vacuums to remove surface imperfections and create the proper concrete surface profile. This step ensures the epoxy bonds fully and evenly.
2. Epoxy Patching
Any cracks or low spots in the concrete were repaired using a two-component epoxy patching material. This created a smooth, consistent base before primer application.
3. Epoxy Primer Application
A high-performance epoxy primer was rolled out across the prepared surface. This layer promotes adhesion and primes the concrete for the next step.
4. Full Aggregate Broadcast
While the primer was still wet, the team broadcast a specialty aggregate across the surface. This helps improve skid resistance and contributes to a thicker, more durable final system.
5. Excess Aggregate Removal and Cleanup
Once cured, the excess aggregate was collected and the surface cleaned, leaving a mechanically bonded texture ready for topcoating.
6. Polyaspartic Pigmented Topcoat
To complete the system, a pigmented polyaspartic topcoat was applied. This sealed the floor into a smooth, continuous surface that’s resistant to chemicals, wear, and moisture.
The Results: Durable, Seamless, and Safe
In just two working days, the CustomCrete team delivered a fully upgraded production floor with:
- Seamless, non-porous surfaces that are easy to clean and sanitize
- Slip resistance to reduce fall risks in high-traffic areas
- A brighter appearance that enhances overall visibility
- Long-term durability with minimal maintenance required
Just as importantly, the company avoided major downtime and was able to resume full operations immediately after curing—without sacrificing performance or safety.
Why Epoxy Floors Are Ideal for Food and Beverage Environments
The Sherwin-Williams Shop Floor System, like many epoxy coatings, is designed to meet the strict demands of food and beverage settings:
- No grout lines or joints: Prevents bacterial harborage
- Chemical resistance: Holds up to aggressive cleaning agents and sanitizers
- Slip-resistant texture: Protects staff and equipment operation
- Fast turnaround: Minimal business disruption during installation
Facilities like breweries, bottling plants, commercial kitchens, and prep areas often choose epoxy because it balances hygiene, safety, and durability without tradeoffs.
Final Thoughts
This case study shows what’s possible when a team prioritizes planning, precision, and product performance. A complete flooring upgrade doesn’t have to mean weeks of shutdowns or complicated logistics. With the right materials and experienced installers, high-impact spaces like bottling facilities can get the flooring they need—quickly and cleanly.
Need help upgrading your production floors? Request a quote with CustomCrete today.
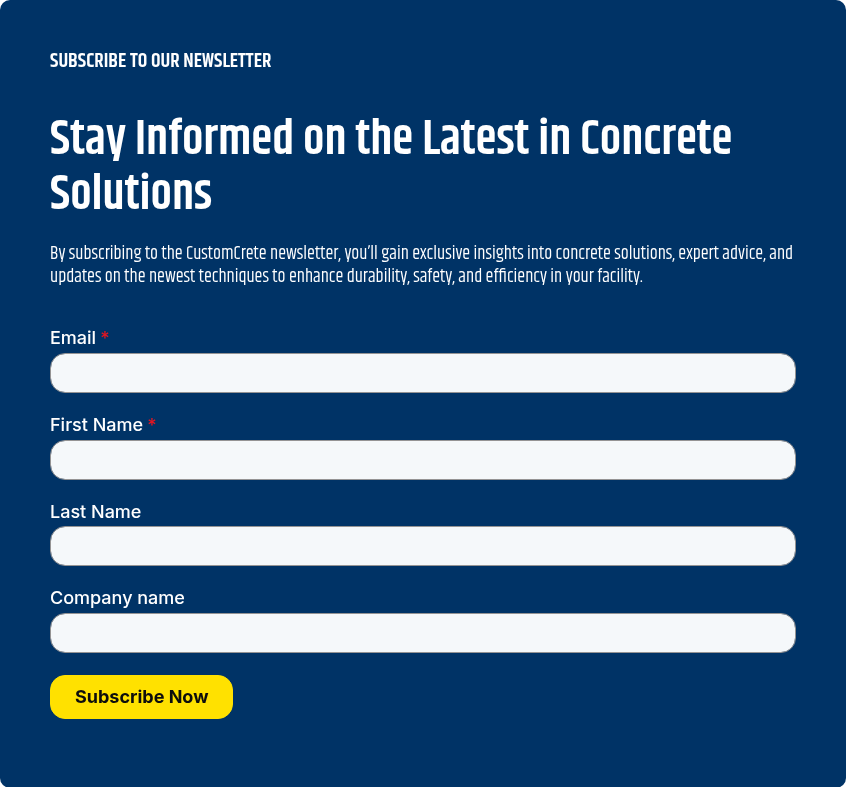