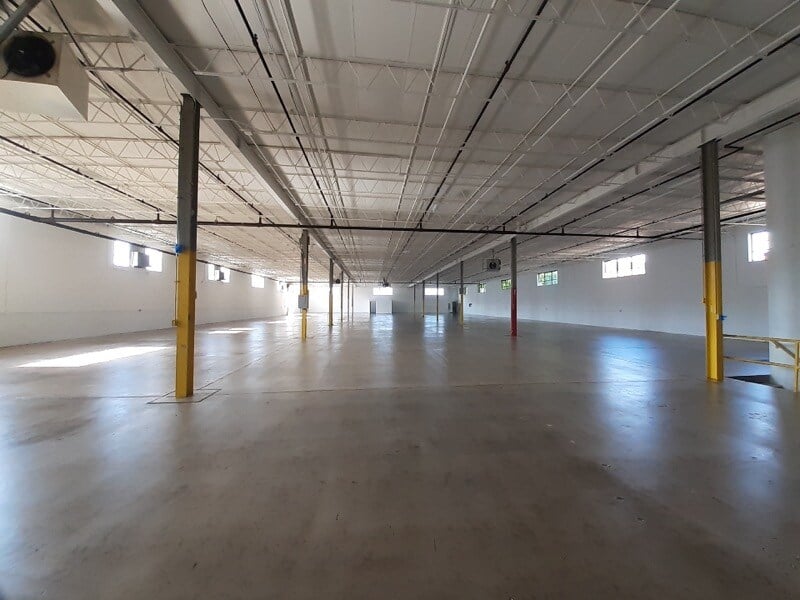
Factories and industrial facilities in Chicago rely on durable flooring solutions to withstand heavy machinery, high foot traffic, and exposure to chemicals and moisture. With years of experience in concrete sealing, CustomCrete has worked with industrial clients across Chicago to provide high-performance sealing solutions tailored to their facility’s specific needs.
Sealed concrete offers long-term protection against wear and tear, prevents dusting, and enhances safety. However, understanding the cost of concrete sealing is crucial for facility managers and decision-makers looking to maintain their investment while managing their budget effectively.
This guide breaks down the key factors that influence the cost of sealing concrete in factories and provides insights into pricing structures to help businesses make an informed decision.
Factors That Influence the Cost of Sealing Concrete
The cost of sealing concrete varies depending on multiple factors, from the type of sealer used to the condition of the existing flooring. Understanding these cost drivers can help facility managers plan their budgets effectively and choose the best sealing solution for their needs.
1. Size of the Facility
The larger the area that needs sealing, the more materials and labor will be required, which impacts the overall cost. Factories with expansive concrete flooring will typically pay less per square foot than smaller facilities due to economies of scale.
2. Type of Sealer Used
Concrete sealers come in different formulations, each with varying levels of protection and cost. Common types include:
- Acrylic Sealers – Affordable and easy to apply, but may require frequent reapplication.
- Epoxy Sealers – Highly durable and resistant to chemicals, but cost more than acrylic options.
- Polyurethane Sealers – Excellent for high-traffic areas with superior abrasion resistance but typically priced higher than other sealers.
- Penetrating Sealers – Designed to protect concrete from within, ideal for moisture-prone areas, but can be expensive.
3. Condition of the Existing Concrete
If the concrete is in poor condition, additional prep work such as repairs, grinding, or cleaning will increase costs. Cracks, oil stains, or surface deterioration require more labor and materials to ensure proper adhesion and effectiveness of the sealer.
4. Application Method
Sealer application methods vary and can impact overall costs. Spray applications are typically faster and more cost-effective, while hand-applied sealers or multiple coating systems require more time and labor, leading to higher costs.
5. Number of Coats Required
Some sealers require multiple coats to achieve the desired level of protection and durability. The more coats applied, the higher the material and labor costs.
6. Location and Environmental Factors
Chicago’s climate, with its fluctuating temperatures and high humidity levels, can affect concrete sealing costs. Additional moisture barriers or specialized sealers may be needed to combat weather-related wear, impacting the final price.
Estimated Cost of Concrete Sealing for Factories in Chicago
The cost of sealed concrete varies depending on the factors mentioned above. On average, industrial concrete sealing in Chicago costs between $1.50 to $5.00 per square foot. Here’s a breakdown based on different sealing options:
- Acrylic Sealers: $1.50 - $3.00 per square foot
- Epoxy Sealers: $2.50 - $4.50 per square foot
- Polyurethane Sealers: $3.00 - $5.00 per square foot
- Penetrating Sealers: $0.25 - $2.00 per square foot
For a 50,000-square-foot factory, sealing costs could range from $75,000 to $250,000, depending on the type of sealer and surface preparation required. Facilities that require premium coatings, additional layers, or extensive floor repairs will be on the higher end of the pricing spectrum.
Long-Term Cost Savings of Sealed Concrete
Investing in sealed concrete not only provides immediate protection but also offers significant financial savings over time. By reducing maintenance costs, extending the lifespan of flooring, and enhancing workplace safety, sealed concrete is a smart choice for factories looking to maximize their investment.
1. Reduced Maintenance and Repairs
Sealing concrete minimizes wear and tear, reducing the frequency of repairs and resurfacing. This lowers long-term maintenance costs compared to unsealed concrete that may develop cracks, spalling, or stains over time.
2. Increased Lifespan of Flooring
A properly sealed concrete floor can last 10-20 years with minimal upkeep, significantly extending the life of the surface compared to untreated concrete.
3. Improved Workplace Safety
Sealed concrete reduces dust accumulation, prevents surface deterioration, and enhances traction, leading to fewer workplace accidents and a safer environment for employees.
4. Protection Against Moisture and Chemicals
Factories that deal with chemical spills, moisture exposure, or heavy machinery benefit from sealed concrete’s ability to resist penetration, preventing costly damage and improving floor longevity.
Is Concrete Sealing Worth the Investment?
For factory owners and industrial facility managers in Chicago, investing in sealed concrete is a cost-effective way to protect their flooring, reduce maintenance expenses, and enhance safety. While the upfront costs may vary depending on the sealer type and floor condition, the long-term benefits far outweigh the initial investment.
To explore the best cost options for your facility and budget, visit our Pricing page and request a consultation today.
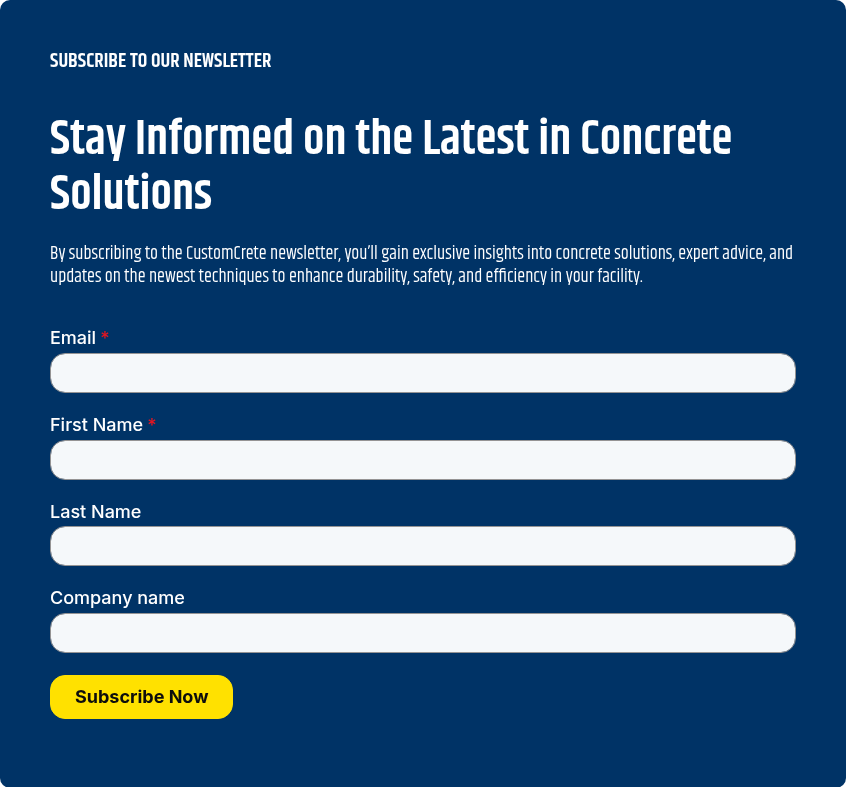