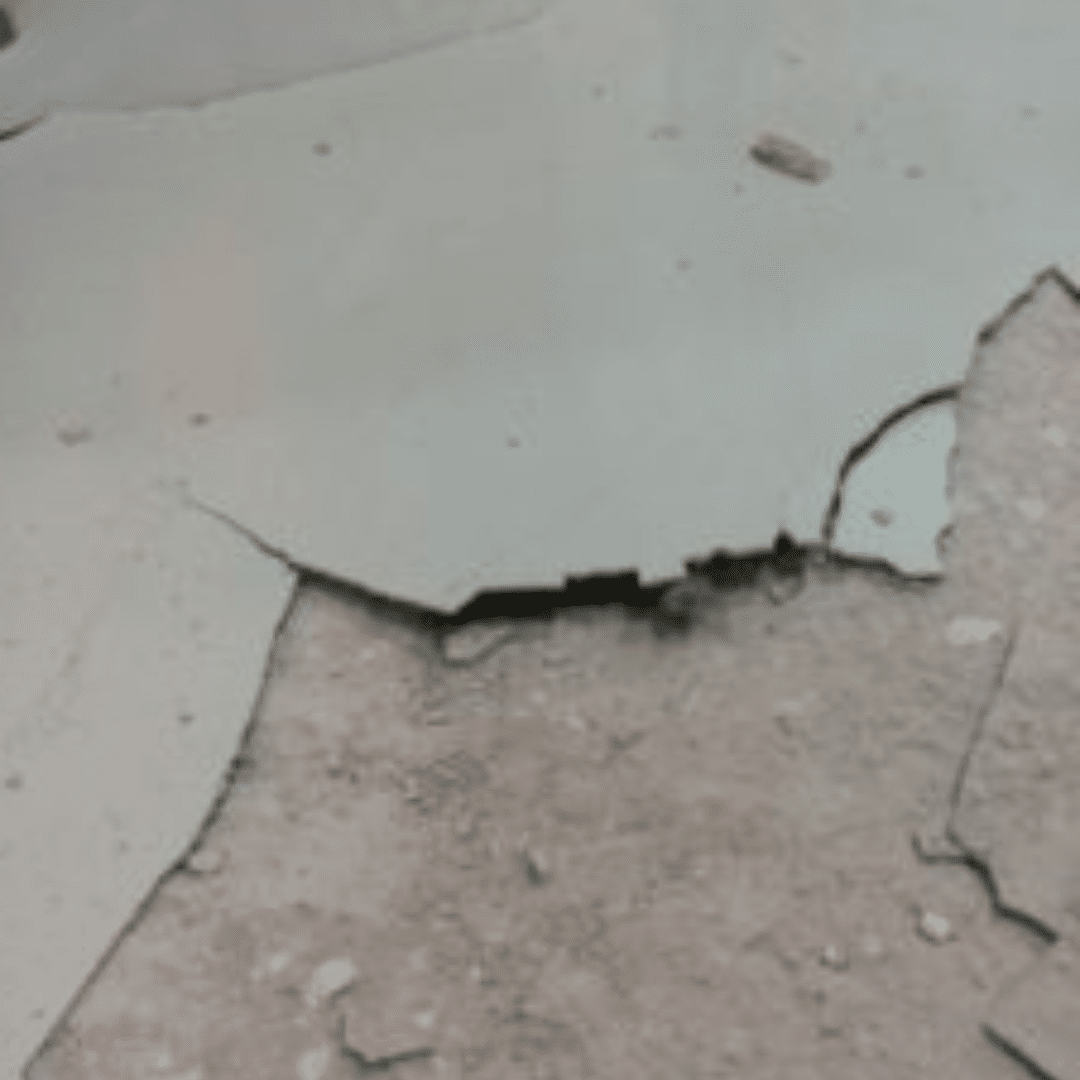
You’ve done the research and decided it's time to invest some money into your concrete floor, and now you're ready for a long-lasting epoxy floor. But there’s one lingering question: “Do I really need a moisture vapor barrier?”
It’s tempting to skip this step, especially when every additional cost makes a difference, but the reality is that moisture vapor can wreck your investment if not properly addressed.
We’ve been in the concrete coating business for years, and we’ve seen first-hand the consequences of skipping moisture protection. At CustomCrete, we’ve helped clients avoid thousands in repair costs by making sure their floors are tested and protected against moisture. Our team has the experience to guide you through this process, and we’ve worked on countless projects where moisture was a major concern.
No one wants to spend more than is absolutely necessary. Putting on an extra coating for moisture might seem like overkill, especially when you learn that not every floor needs this protection. But gambling on your concrete's moisture levels, even with proper testing, can sometimes lead to delamination of your brand-new coating, costing you thousands in repairs down the road.
There are many options available, and it’s easy to get lost in the details. Do I go with a barrier or not? Should I test for moisture vapor, and is that a sure thing? You could choose a coating like urethane cement, which is immune to moisture vapor damage, or pick a breathable solution like polished concrete, which won’t be affected. But for epoxy or sealed concrete coatings, moisture is a major consideration.
In this article, we’ll break down the cost of moisture vapor barriers and the testing options available so you can make an informed decision and safeguard your flooring project from expensive failures.
Why Moisture Matters in Concrete Coatings
Concrete is porous, and even though it seems solid, water vapor can and will seep through. When this happens, any coating applied on top—whether it’s epoxy, a sealant, or another finish—is at risk of peeling away, a problem called delamination. Essentially, water vapor rises from within or under the concrete, pushing the coating off the surface. The result? You’ve got a costly repair on your hands, and the original finish is flaking off and ruined.
Hydrostatic vs. Water Vapor:
Hydrostatic Pressure: In the context of concrete slabs or floors, hydrostatic (water) pressure occurs when liquid water enters the structure through cracks, wall-to-floor joints, or other construction defects. This water is visible on interior floors as ponding or pooling (excluding rainwater entering through windows or doors).
Water Vapor: Water vapor refers to water in its gaseous state, which can easily pass through semi-permeable materials like concrete. Unlike hydrostatic pressure, water vapor isn’t visible—there are no wet spots or pooled water. It permeates the substrate but cannot be seen.
The problem is that not every concrete floor shows visible signs of moisture. It's possible moisture is only present intermittently. So, you may not notice an issue until it’s too late and the coating has already started to fail. That’s where moisture mitigation comes into play. It offers a crucial barrier between your concrete and its finish, preventing moisture from penetrating the surface and ensuring your coating stays intact for years.
What’s the Real Cost of Skipping a Moisture Vapor Barrier?
So, how much will a moisture vapor barrier cost you? Generally, moisture vapor barriers cost between $2 and $3 per square foot, on top of the cost of the coating you are looking to apply.
For larger industrial or commercial projects, you may get a discount per square foot, but smaller spaces may run slightly higher. Ultimately, it’s an investment designed to protect you from much larger costs down the road. Repairs due to delamination can balloon costs to thousands of dollars, especially if a full removal and reinstallation of the floor coating is required.
Let’s break down the specific factors that can influence the final price:
- Size of the area: The larger the surface area, the more materials and labor required. However, large jobs often come with a lower cost per square foot, especially in industrial settings.
- Condition of the concrete: If your concrete floor is in poor shape, with cracks, chips, or spalling, you may need additional surface preparation, which can add to the overall cost.
- Accessibility: Hard-to-reach areas, such as floors in basements or spaces that require extra labor, will raise the price due to the complexity of the work.
Testing for Moisture in Concrete: Is It Worth It?
Not every concrete floor will require a moisture vapor barrier, and that’s where moisture testing comes in. While no test is 100% foolproof, testing provides a semi-reliable gauge of whether or not you’re at risk for moisture problems. At CustomCrete, we offer three main types of tests, each with its own price range:
Tramex Surface Testing:
This test measures moisture at the surface level of the concrete. It's a quick way to assess moisture content and give you an immediate read on the potential risk. This method is non-invasive but not very accurate.
Price: Free
RH (Relative Humidity) Probe Testing:
For a more in-depth analysis, the RH test uses probes to measure the moisture levels within the surface of your concrete. By drilling holes and inserting probes at various depths, this method provides a clearer picture of how much moisture is trapped within, which could eventually rise and impact the coating.
Price: $150 per 1,000 square feet
Calcium Chloride Testing:
This test measures the moisture vapor emissions coming through the concrete. A small dish of calcium chloride is placed on the floor and sealed, and over 72 hours, it absorbs any moisture in the air above the surface. Afterward, the dish is weighed to determine how much moisture vapor has been emitted.
Price: $150 per 1,000 square feet
Each of these tests provides valuable information about the condition of your concrete and helps determine whether a moisture vapor barrier is necessary. However, testing isn’t a perfect science. Many factors can influence moisture levels, including environmental conditions, changes in weather, and the age of the concrete. Ultimately, you’re controlling for risk.
Conclusion: Protect Your Investment with a Moisture Vapor Barrier
At the end of the day, protecting your investment is the name of the game. Sure, skipping the moisture vapor barrier might save you some money upfront, but if you decide to go with epoxy or sealed concrete coatings without it, you could be opening the door to significant and expensive problems later on.
Testing can give you more data to make an informed judgment, but no test is perfect, and ultimately, it can be a gamble without the moisture vapor barrier. We want you to understand the risks so you can make the best decision for your flooring project.
Remember, you have options. You can avoid moisture issues altogether with choices like urethane cement or polished concrete, or you can install a moisture vapor barrier and have peace of mind.
Ready to get started? Still have questions about moisture testing or moisture vapor barriers? Contact CustomCrete today. We’re here to help you make the smartest decision for your floor… and your wallet.
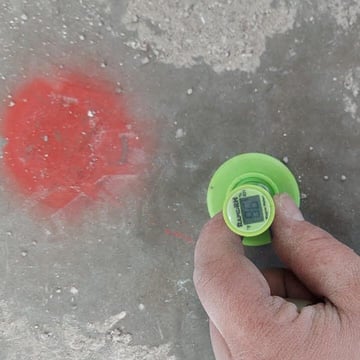