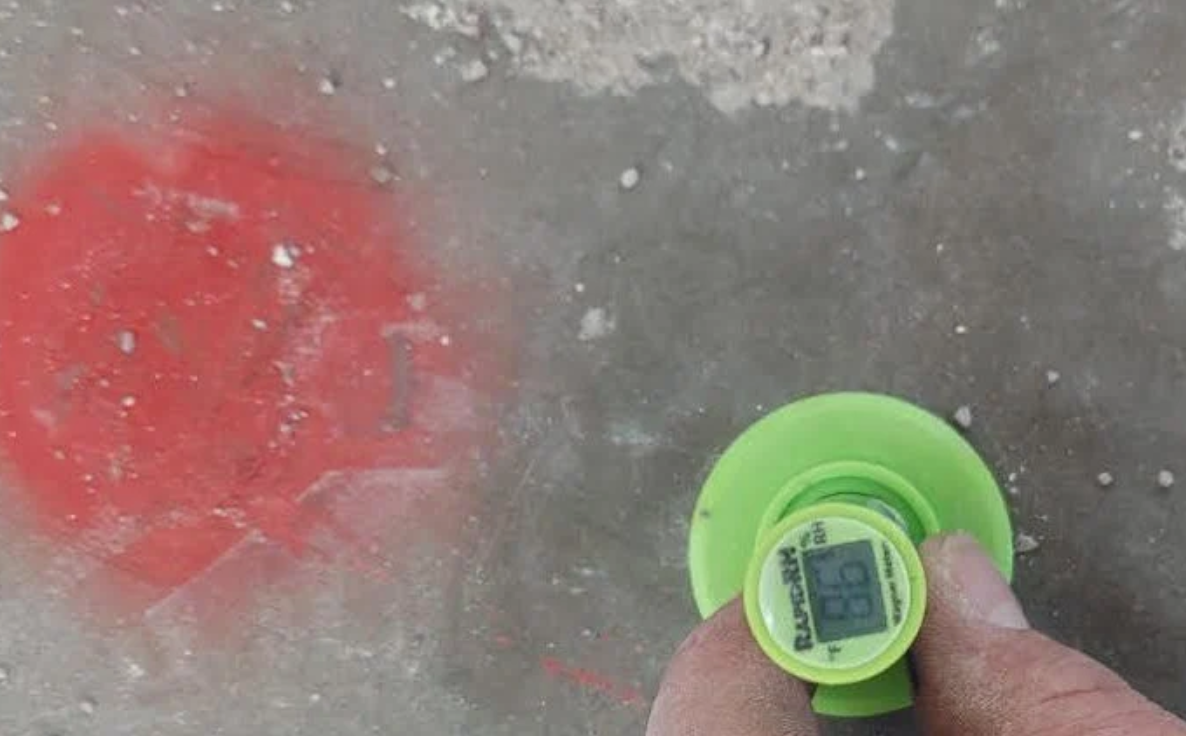
Moisture-related issues are one of the leading causes of failure in concrete floor coatings. Whether you're running a food processing plant, warehouse, or manufacturing facility, ignoring the presence of moisture vapor in your concrete slab can put your investment—and safety—at risk.
That’s where a moisture vapor barrier comes in. But while these barriers offer powerful protection, they aren’t always necessary—and they do come with some trade-offs. Below, we break down the pros and cons to help you make a well-informed decision for your industrial flooring project.
What is a Moisture Vapor Barrier (MVB)?
A moisture vapor barrier (sometimes called a vapor mitigation system) is a specially formulated coating applied directly to a concrete slab. Its primary purpose is to block or reduce the amount of moisture vapor moving from the ground up through the concrete. Without this barrier, water vapor can build up pressure beneath the surface, causing coatings to bubble, peel, or delaminate over time.
Moisture vapor barriers are commonly used under high-performance coatings like epoxy, urethane, and polyaspartic systems, especially in facilities where performance and longevity are critical.
Why Moisture Matters in Concrete Floors
Concrete might seem solid, but it’s actually porous—meaning moisture can move through it like a sponge. Even if your space feels dry, vapor can be moving upward from the subgrade below. This is particularly common in older buildings, high-humidity areas, or slabs without a proper vapor retarder underneath.
When that moisture reaches the surface and becomes trapped under a floor coating, it can lead to problems such as:
- Blistering or bubbling of the surface
- Delamination, where the coating separates from the substrate
- Microbial growth in food and beverage or healthcare facilities
- Coating discoloration or performance loss over time
Moisture vapor barriers are designed to stop this from happening by sealing the slab and allowing for a more stable, longer-lasting floor.
The Pros of Moisture Vapor Barriers
Moisture vapor barriers provide significant benefits for concrete flooring in industrial and commercial spaces. From preventing structural damage to enhancing flooring performance, these barriers are a valuable investment for many businesses. Below are some of the key advantages of using an MVB.
1. Prevents Coating Failure
Perhaps the biggest advantage of using a moisture vapor barrier is the protection it offers your topcoat. By locking moisture beneath the surface, it prevents bubbling, peeling, and other issues that can ruin the integrity of your floor system.
2. Extends Floor Lifespan
By reducing the impact of vapor pressure and water-related damage, an MVB can significantly increase the lifespan of your coating system. This means fewer repairs, less downtime, and a better return on investment over the long term.
3. Ideal for High-Moisture Conditions
If your facility is located in a humid environment or built over a slab with high relative humidity, a moisture vapor barrier can be an essential tool in maintaining performance. This is especially true in cold storage areas, food production facilities, and places that undergo frequent cleaning or steam exposure.
4. Compatible with Many Coating Systems
Modern moisture vapor barriers are designed to work with a variety of industrial coatings—including epoxy, urethane, and polyaspartic systems. This makes them a flexible option that can be built into a wide range of flooring solutions.
The Cons of Moisture Vapor Barriers
While moisture vapor barriers offer significant benefits, they also come with certain challenges that businesses should consider before installation. Below are some potential drawbacks to keep in mind when deciding whether an MVB is the right choice for your facility.
1. Increased Cost
Because moisture barriers are a separate product (and often require additional labor), they add to the total cost of the flooring system. While this cost often pays off in the long run, it’s important to factor it into your budget when evaluating options.
On average, the cost to install a moisture vapor barrier ranges from $2 to $4 per square foot, depending on factors such as material thickness and labor requirements. For a 1,500-square-foot area, this translates to an investment between $3,000 and $6,000. While this may seem substantial, it's important to weigh these initial costs against the long-term benefits of preventing moisture-related flooring issues.
2. Added Installation Time
Installing a moisture vapor barrier adds an extra step in your flooring project. Depending on your timeline, this could add 1–2 days to the schedule—especially if the product requires cure time before topcoats are applied.
3. Not Always Needed
Not every slab needs a moisture vapor barrier. If your concrete has already been tested and falls below critical moisture thresholds, skipping the MVB might be a smarter choice. That’s why moisture testing is essential before deciding whether to include one.
Is a Moisture Vapor Barrier Right for Your Facility?
The best way to determine whether your facility needs a moisture vapor barrier is by conducting a professional moisture test. At CustomCrete, we use industry-standard methods like:
- Tramex surface testing for a quick initial read
- RH probe testing to assess moisture deeper in the slab
- Calcium chloride testing to measure vapor emission over time
If results show high levels of moisture—typically above 75–85% relative humidity or more than 3 lbs/1000 sq. ft./24 hrs of vapor emission—a moisture vapor barrier is strongly recommended before applying any floor coating.
Conclusion: Protecting Your Floors with the Right Solution
A moisture vapor barrier can be a smart, proactive investment—especially in high-performance environments or buildings with known moisture concerns. While it adds some cost and time upfront, it dramatically reduces the risk of coating failure, improves durability, and protects your facility from hidden threats underneath your floor.
Need Guidance on Moisture Testing or Vapor Barriers? To learn more, visit our solutions page, "Moisture Mitigation & Testing".
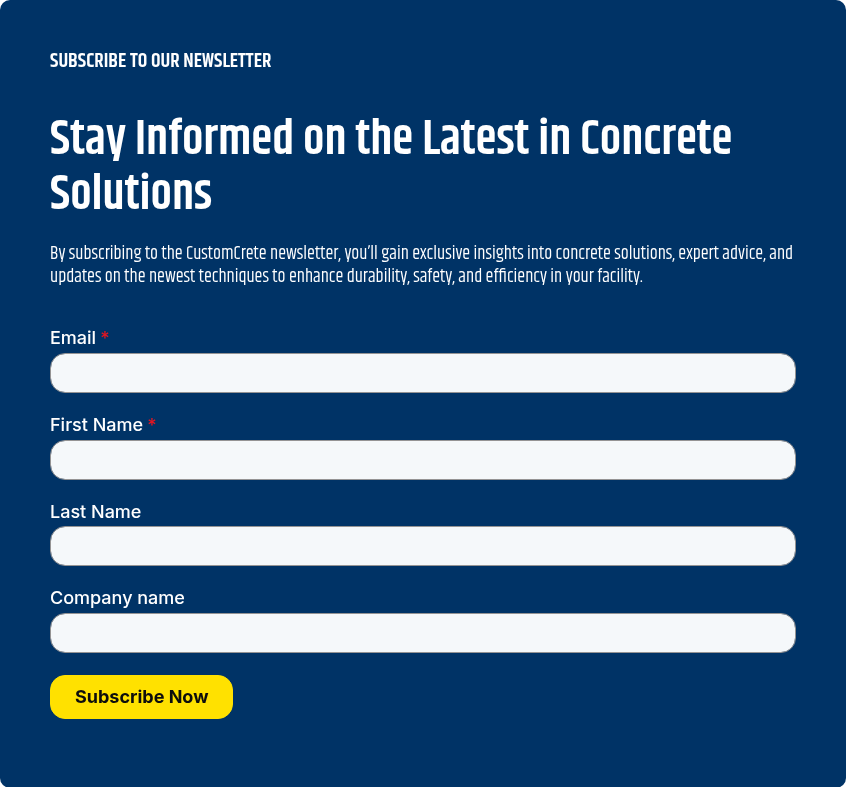