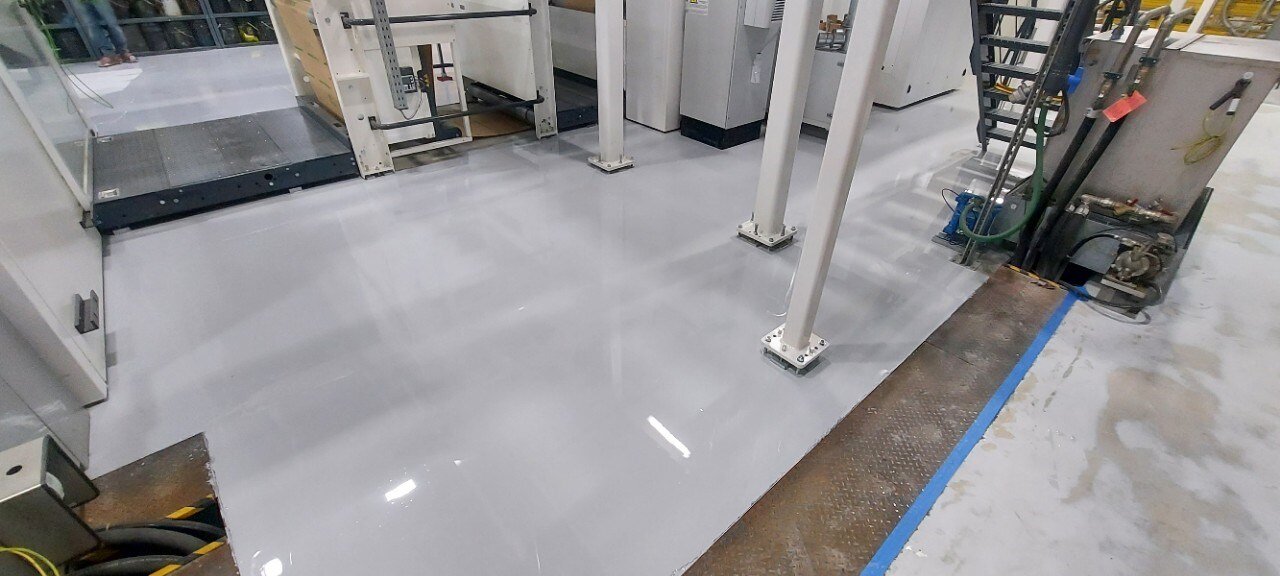
Choosing the right topcoat is one of the most important decisions in any concrete flooring system. Whether you're sealing a warehouse, production area, or commercial facility, the topcoat serves as your floor's frontline defense—against chemicals, foot traffic, impacts, UV exposure, and more.
Among the available options, the polyurethane topcoat is widely respected for its toughness, flexibility, and visual appeal. But it’s not always the perfect fit. In this post, we’ll break down the key advantages and potential drawbacks of polyurethane topcoats so you can decide whether it’s the right solution for your space.
What is Polyurethane Topcoat?
A polyurethane topcoat is a protective layer applied over concrete floor coatings—most commonly over epoxy or broadcast systems. It creates a thin but durable shield that helps resist abrasion, chemicals, UV rays, and wear. Depending on your project, it may be used as part of a multi-layer coating system or as the final step in an industrial-grade floor finish.
Polyurethane topcoats are available in both water-based and solvent-based formulas and can be applied in matte, satin, or high-gloss finishes depending on your facility’s needs and aesthetics.
The Pros of a Polyurethane Topcoat
Polyurethane topcoats offer a range of benefits that make them a popular choice for protecting and enhancing surfaces in commercial settings.
1. Excellent Abrasion Resistance
One of polyurethane’s biggest advantages is its resistance to surface abrasion. In high-traffic areas—such as loading docks, warehouses, or assembly lines—a polyurethane topcoat helps preserve the integrity of your floor. This protection minimizes surface scratching, chipping, and dulling over time.
2. UV Stability and Color Protection
Unlike standard epoxies, polyurethane topcoats are UV stable, meaning they won’t yellow or degrade when exposed to sunlight. This makes them an ideal choice for spaces with natural lighting or exterior exposure. It also helps preserve the color and clarity of decorative flooring systems, such as flake or quartz broadcast finishes.
3. Flexibility for Minor Substrate Movement
Polyurethane has a higher level of elasticity compared to rigid epoxies. This flexibility allows it to accommodate slight movement in the slab or coating system—particularly useful in environments where temperature fluctuations or equipment vibrations are common.
4. Fast Recoat Times and Curing
Many polyurethane systems offer quick dry times and recoat windows, which can speed up project timelines and reduce facility downtime. This is especially beneficial in fast-paced operations that can’t afford extended closures.
5. Chemical Resistance
Polyurethane topcoats offer strong resistance to a wide range of chemicals, including cleaning agents, oils, and fuels. While not quite as chemical-resistant as Novolac epoxies, they’re more than sufficient for most industrial and commercial environments.
6. Low Maintenance Costs
With a long lifespan, polyurethane coatings require fewer repairs or reapplications, leading to lower long-term costs. Facilities can save on labor and material expenses over time, making polyurethane an economically sound investment.
Properly applied polyurethane topcoats can last several years without the need for frequent touch-ups or replacements, providing continuous protection with minimal upkeep. An additional benefit is to add a high-wear additive that extends the lifespan of your floors and creates a preferred texture.
The Cons of Polyurethane Topcoat
While polyurethane topcoats provide excellent protection and durability, they also come with some drawbacks that are important to consider before application.
1. Requires Professional Application
Polyurethane topcoats can be finicky to apply and may be sensitive to temperature and humidity during installation. Uneven application or improper curing conditions can lead to bubbling or inconsistent finishes, so it’s not recommended for DIY projects. A professional installation ensures proper adhesion and performance.
2. Lower Thickness Than Epoxy
Polyurethane is typically applied in thinner coats than epoxy. While this makes it more flexible, it also means it’s not as effective for filling small surface imperfections or leveling rough slabs. That’s why it’s most often used on top of another coating system rather than as a standalone solution.
3. Less Impact-Resistant Than Urethane Cement
While polyurethane handles abrasion well, it may not perform as well in extremely heavy-duty environments where impact resistance is critical—such as with repeated drops of heavy tools or pallet traffic. In these cases, a urethane cement or high-build epoxy may be more appropriate.
4. Slightly Higher Cost Than Basic Topcoats
Due to its enhanced chemical resistance, UV stability, and flexible properties, polyurethane can be more expensive than basic epoxy or acrylic sealers. However, many facilities find the extended durability and protection are well worth the additional upfront investment.
When to Use a Polyurethane Topcoat
A polyurethane topcoat is a great choice when you need:
-
A durable, long-lasting finish that resists surface wear
-
UV protection for indoor-outdoor spaces or sunlit interiors
-
A flexible top layer over more rigid systems like epoxy
-
A protective finish over decorative flake or quartz systems
-
Moderate chemical resistance without the cost of specialty coatings
It’s especially effective in spaces like:
-
Distribution centers
-
Warehouses
-
Manufacturing plants
-
Auto service bays
-
Retail stores with polished or decorative flooring
Is Polyurethane the Right Topcoat for Your Facility?
Choosing the right topcoat often comes down to balancing priorities: abrasion resistance, chemical exposure, environmental conditions, and aesthetics. If your space demands high performance, visual clarity, and long-term protection, a polyurethane topcoat might be your best bet.
That said, it’s not a one-size-fits-all solution. Spaces with extreme thermal shock, standing water, or heavy impact may need something more robust—like urethane cement or specialized epoxy systems.
Working with a knowledgeable contractor can help you weigh your options and determine which floor coating system will deliver the best performance for your unique facility. If youre ready to take the next step, request a quote to see if polyurethane is the right choice for you.