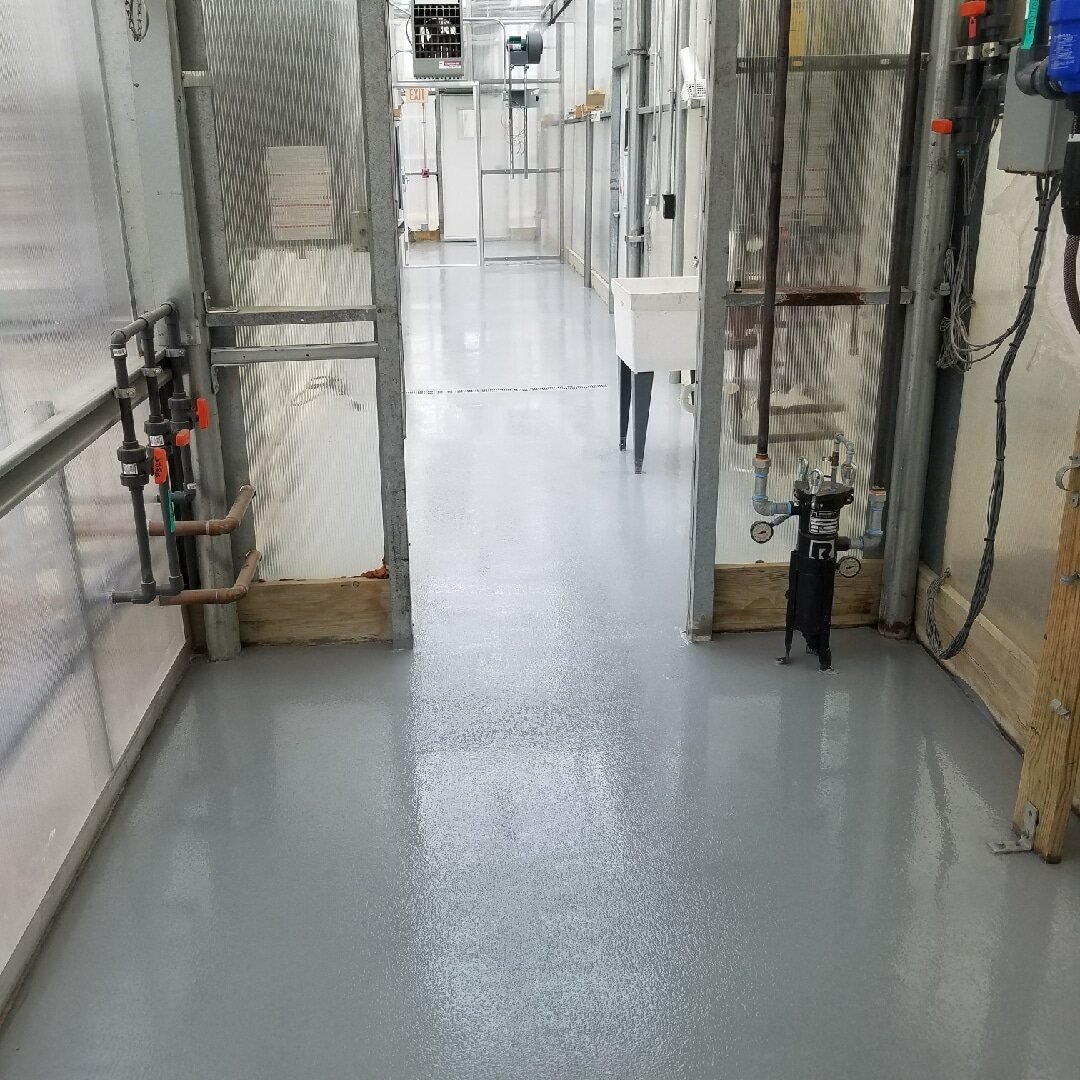
Upgrading your business space can feel overwhelming, especially when it comes to choosing the right industrial floor coating. One wrong decision can lead to serious problems like frequent repairs, safety hazards, and even costly operational downtime. Your floors face daily wear and tear from foot traffic, heavy machinery, spills, and exposure to chemicals. Without the proper protection, deterioration is inevitable, leading to headaches you just don’t need.
We understand the stress these issues cause and the impact they can have on your bottom line. That’s why selecting the right flooring is so important. Whether it’s epoxy, polyurethane, acrylic, or polished concrete, each option comes with unique benefits. But choosing the wrong one could mean dealing with early damage, unexpected costs, and more downtime than you can afford.
Making an informed decision now will save you time, money, and unnecessary stress. With 20 years of commercial and industrial flooring experience, CustomCrete is here to help you choose the best solution tailored to your business’s needs, so you can protect your floors and keep your operations running smoothly.
Understanding the Different Types of Industrial Floor Coatings
Each industrial floor coating has its own advantages, and the right choice depends on your business's specific needs. Let’s take a look at the most common options available:
Epoxy Floor Coatings
Epoxy is widely known for its strength and durability, making it a top choice for businesses that deal with heavy machinery or high foot traffic. This coating is highly resistant to chemicals, scratches, and general wear and tear.
Epoxy can be customized with various finishes, including high-gloss, colors, and patterns, making it a versatile option for different environments. However, one of its important to keep curing time in mind. Epoxy typically takes 12 hours to set up for foot traffic, however quick cure options are available.
Polyurethane and polyaspartic Floor Coatings
This coating is more resistant to scratches and scuffs than epoxy, which is why it’s a popular choice for commercial spaces where appearance is important, such as showrooms or retail spaces.
Polyurethane also cures within about 12 hours for foot traffic, however, if minimizing downtime is a priority, there are options available. Additionally, it’s resistant to UV light, making it an excellent choice for outdoor applications or areas exposed to direct sunlight and indoor lighting (which also emits some UV).
Polished Concrete
Polished concrete is another great option for businesses looking for an affordable and durable flooring solution. Unlike epoxy or polyurethane, polished concrete does not require any additional coatings.
The process involves grinding down the existing concrete slab and polishing it to create a smooth, glossy finish. This makes it an eco-friendly option since it uses the existing material.
Polished concrete is highly durable, low maintenance, and can last for decades in the right conditions. It’s perfect for warehouses, factories, and commercial spaces that need a cost-effective yet tough solution.
Acrylic Floor Coatings
Acrylic coatings are a more budget-friendly solution, offering ease of application and reapplication. While not as durable as epoxy or polyurethane, acrylic coatings are ideal for lower-traffic areas or businesses looking for a quick, temporary solution.
They’re often used in commercial spaces where aesthetics are important, but heavy-duty protection is not required. If you’re looking for a cost-effective floor refresh that won’t break the bank, acrylic could be the way to go.
Factors to Consider When Choosing Your Industrial Floor Coating
With so many options available, how do you decide which industrial floor coating is right for your space? Here are a few key factors to consider:
Traffic and Usage
Think about what your floor will go through on a daily basis. Will it face foot traffic, heavy machinery, or both? The more wear and tear your floor experiences, the more durable the coating needs to be. Epoxy and polyurethane are excellent for high-traffic and machinery-heavy environments, while polished concrete is a great all-around solution for both durability and affordability.
Chemical Resistance
If your business frequently deals with chemicals, spills, or solvents, you’ll need a coating that can handle these conditions without breaking down. Epoxy and polyurethane are known for their chemical resistance, making them ideal for warehouses, manufacturing facilities, and food processing plants. Polished concrete also offers some resistance to spills but may not be as strong against chemicals without a sealer.
Aesthetic Requirements
The appearance of your floor can impact the overall look of your business. Retail spaces, showrooms, and offices may require a floor that not only performs well but also looks professional.
Polyurethane and epoxy can be customized with different finishes and colors, offering flexibility in design. Polished concrete, on the other hand, offers a sleek, modern look with a glossy finish, perfect for those who want a clean, industrial feel without the need for added coatings. Polished concrete also can be stained, giving you a wider range of options.
Installation Time and Downtime
How much downtime can your business afford during the installation process? Epoxy coatings often require a longer curing time, while polyurethane and acrylic coatings can be installed more quickly.
Polished concrete, while durable, also requires a significant amount of time for grinding and polishing. If minimizing downtime is essential, polyurethane or acrylic might be better options.
Budget
Your budget will also play a major role in your decision. Epoxy and polyurethane coatings tend to have higher upfront costs but offer long-term savings due to their durability and low maintenance.
Acrylic coatings are cheaper initially but may require more frequent maintenance and reapplication, which can add up over time. Polished concrete is often the most cost-effective option, providing durability without the need for expensive coatings.
Durability and Maintenance: The Key to a Lasting Industrial Floor
The durability of your industrial floor coating will dictate how often you need to perform maintenance or repairs. Epoxy, polyurethane, and polished concrete are all highly durable options, standing up to heavy machinery, foot traffic, and chemical exposure.
However, acrylic coatings, while less durable, are easier to reapply when necessary.
Maintenance is another important factor. Epoxy and polished concrete are low-maintenance, requiring only regular cleaning with mild cleaners.
Polyurethane and polyaspartic are very durable and it’s generally easy to maintain.
Acrylic coatings, while simple to apply, will need more frequent touch-ups in high-traffic areas.
Safety Considerations: Chemical and Slip Resistance
Safety is a top priority for any industrial space, and the right floor coating can help reduce accidents. Both epoxy and polyurethane coatings offer excellent chemical resistance, protecting your floor from spills that could cause damage or create hazardous conditions.
Polished concrete, while resistant to some chemicals, may need a sealer for stronger protection.
Slip resistance is also critical, particularly in areas where spills or moisture are common. Epoxy, polyurethane, and acrylic coatings can be enhanced with anti-slip additives to improve traction.
Balancing Cost with Quality: The Long-Term Benefits
While it may be tempting to choose the cheapest option, investing in a high-quality floor coating will pay off in the long run.
Epoxy and polyurethane coatings might have higher upfront costs, but their durability and low maintenance requirements make them a cost-effective choice over time.
Polished concrete, being an inexpensive option, provides a durable and long-lasting solution without the need for additional coatings. It’s an eco-friendly and budget-conscious option that can meet the needs of many industrial spaces.
On the other hand, cheaper options like acrylic may save you money initially but require frequent reapplication and maintenance, which can add to your overall expenses. Polished concrete offers a sweet spot between affordability and performance, making it a smart investment for many businesses.
What to Expect During Installation of an Industrial Floor
Installing an industrial floor coating or polishing concrete involves several steps.
First, the area needs to be profiled and any existing coatings removed. For epoxy, polyurethane, and acrylic coatings, any cracks or imperfections in the concrete must be repaired before applying the coating.
Each coating layer must cure before the next is applied, with final curing times varying depending on the type of coating.
Polished concrete requires a different process. The surface is ground down using progressively finer diamond grinders until the desired finish is achieved. Then it is treated with a chemical densifier and deduster. This process can take time but results in a highly durable, low-maintenance floor.
Choosing the Right Industrial Floor Coating
Selecting the right industrial floor coating for your business comes down to understanding your specific needs. Think about the traffic, chemical exposure, and aesthetic requirements of your space.
Consider how much downtime you can afford during installation and how much you’re willing to invest upfront.
Epoxy and polyurethane offer high durability and customization options, while polished concrete provides a cost-effective, low-maintenance solution that can last for decades.
No matter which option you choose, investing in the right floor coating will protect your floors, improve safety, and ultimately save you money in the long run. If you’re ready to explore your options consider see our full list of services.
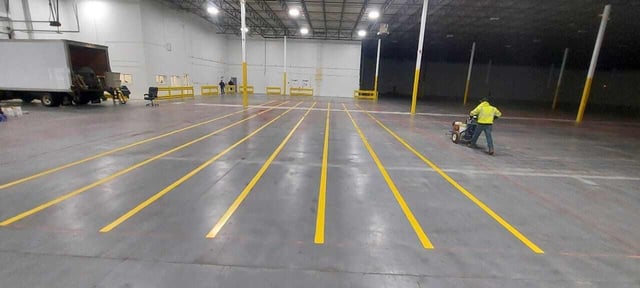