Cost of Urethane Concrete: The Best Option To Address Thermal Shock
August 30th, 2024
4 min read
By Tom Dassie
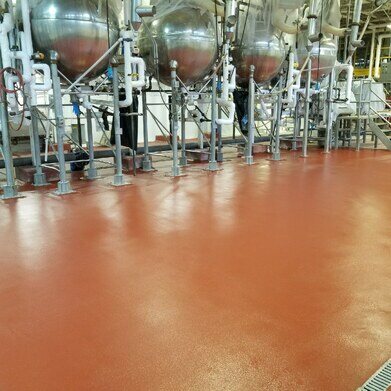
Coating delamination is a hazard to food plants and their managers. You work to keep your facilities clean and up to code. You scrub your floors with hot water, only for thermal shock and sudden temperature changes to cause your concrete floor coating to peel.
At CustomCrete we understand these challenges and our team of industrial flooring experts have a solution for your specific situation. If your space is subject to wide swings in temperature and requires flooring that can take heavy use and abuse, urethane concrete is the solution for you.
Urethane concrete, also known as urethane cement, polyurethane cement, polyurethane concrete, and cementitious urethane, is a heavy duty industrial flooring solution that resists temperature changes and heavy use. For this solution, polyurethane and cement is applied to a concrete surface to make it stronger, safer, easier to clean, and longer lasting. A surface coating is often applied with quartz aggregate. This adds slip resistance and wearability, eases cleaning, and customizes the look of your flooring.
Here's a quick breakdown of expected costs. It covers both per square foot and for a standard 5,000-square-foot area found in commercial kitchens, production lines, and breweries. Larger areas often mean lower costs per square foot. Smaller areas tend to raise the price per square foot, as the mobilization costs are spread over a smaller area.
As a disclaimer: Every job is different. This article assumes a standard project using a basic selection of urethane concrete products. It should provide a rough estimate for projects, not a guaranteed quote. There are many types of urethane concrete. It's impractical to list every option and price here. This is just a baseline tool to give you some idea of the costs so you can start to make an informed decision. With that in mind, let’s dive into the essentials...
Price Ranges for Different types of Urethane Concrete
pricing of urethane cement is unique to each project. These ranges should give you some idea of what to expect...
Urethane Cement SL
- Cost per Square Foot: $7.00-$12.00
- Total for 5,000 sq ft: $35,000 to $60,000
Urethane Cement SL is a cost-effective option for resistance to thermal shock. It’s thinner, about 1/8 to 3/16 inch, applied directly over your concrete slab. It’s a great choice for many commercial spaces.
Urethane Cement HF
- Cost per Square Foot: $10.00-$15.00
- Total for 5,000 sq ft: $50,000 to $75,000
Urethane Cement HF application is the most durable, heavy-duty option. It’s applied as a 1/4 to 3/8-inch coating on top of your concrete slab. This option is perfect for businesses needing a floor to handle heavy use and abuse.
Note: You can make the coating stronger by adding iron aggregate.
Urethane Cement MD
- Cost per Square Foot: $9.00-$13.00
- Total for 5,000 sq ft: $45,000 to $65,000
Urethane Cement MD application is a Medium Duty coating that’s between 3/16 and 1/4 inch thick. It’s perfect for businesses that need high resistance to thermal shock and heavy wear. This is the most popular option and offers flexibility for customizing the floor’s texture.
Decorative Flake or Quartz
- Cost per Square Foot: $15-$20
Total for 5,000 sq ft: $75,000 to $100,000
Decorative flakes or quartz are applied over urethane cement to add color, texture, and extra traction. There are many options available to match both the look and function you need. A clear seal coat is added on top to hold everything in place and provide a glossy finish
As a disclaimer: Every project is unique. This guide provides general estimates, but it’s not a guaranteed quote. There are many types of urethane concrete, so it’s not practical to list all the options and prices here. This will give you a good starting point to understand the costs, but you’ll want to get a more specific quote for your project.
Additional Costs Industrial Floor Coatings can Incur
While the above ranges give you a good starting figure, the final cost of your project will depend on several other factors as well:
Size of the Area
Larger projects typically reduce the cost per square foot, while smaller jobs will increase pricing per square foot. For larger areas, material costs decrease, and labor efficiency improves. Our crew can work continuously without frequent stops or a need for moving equipment. This leads to lower labor costs per square foot.
Conversely, smaller projects may need more precision and time. Many edges, obstacles, or tight spaces can increase the cost per square foot as our crew must work around these. Additionally, the fixed costs of mobilization, equipment setup, and cleanup are spread over a smaller area, which increases the cost per unit for smaller jobs.
Surface Preparation
Concrete needs to be profiled between CSP (concrete surface profile) between 3 and 5. For floors with certain surface imperfections and gunk, such as old epoxy, vinyl glue, and carpet glue remnants, a process called shot blasting or scarification will be employed to prepare the surface for the new treatment. The more prep we have to do, the more costs we associate.
Project Complexity
The more intricate the application process, the higher the potential cost. If we have to work around fixtures, around or under large machines, tight corners, or narrow thruways, this will tend to increase the pricing. A tank area with fixed equipment, twists, and obstacles will increase complexity. More labor for our team increases the costs. A simple warehouse with no obstacles will be less complicated, take less time, and cost less money.
Accessibility
For Urethane flooring CustomCrete focuses primarily on large food preparation spaces, factory floors, refrigerated areas, warehouses, and commercial flooring. This means mostly open spaces without a great deal of obstruction. Our equipment requires more labor to set up if your project is on a high floor or obstructed.
For example, if your space is located in a high-rise building with limited elevator access, our team will need to factor in additional time and labor to move equipment and materials to the site. Conversely, if there is a loading dock, freight elevator, or ramp available, this will bring prices down for your project. Easy access allows us to set up quickly, minimizing delays and reducing labor costs, which ultimately translates to a lower cost for your project.
Additionally, if the site has sufficient space for staging equipment and materials, this further streamlines the process and can lead to more savings.
Finding the best solution for your needs with CustomCrete
At CustomCrete, we’re here to help you find the best solution for your project. We want you to have all of the information you need going in. Whether you need basic protection or heavy-duty durability, we can guide you to the right choice for your situation, and these tools are here to help you even if you don’t go with us.
Ready for a quote?
If you’re ready to get a precise quote for your project, the next step is simple: Contact us for a quote. We’ll walk you through the options and make sure you get exactly what you need without any surprises.
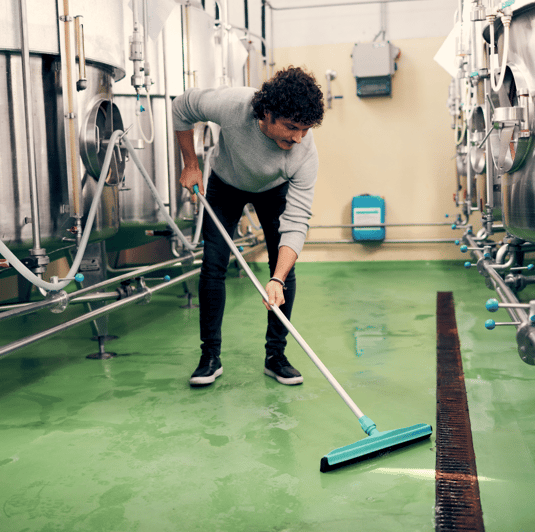