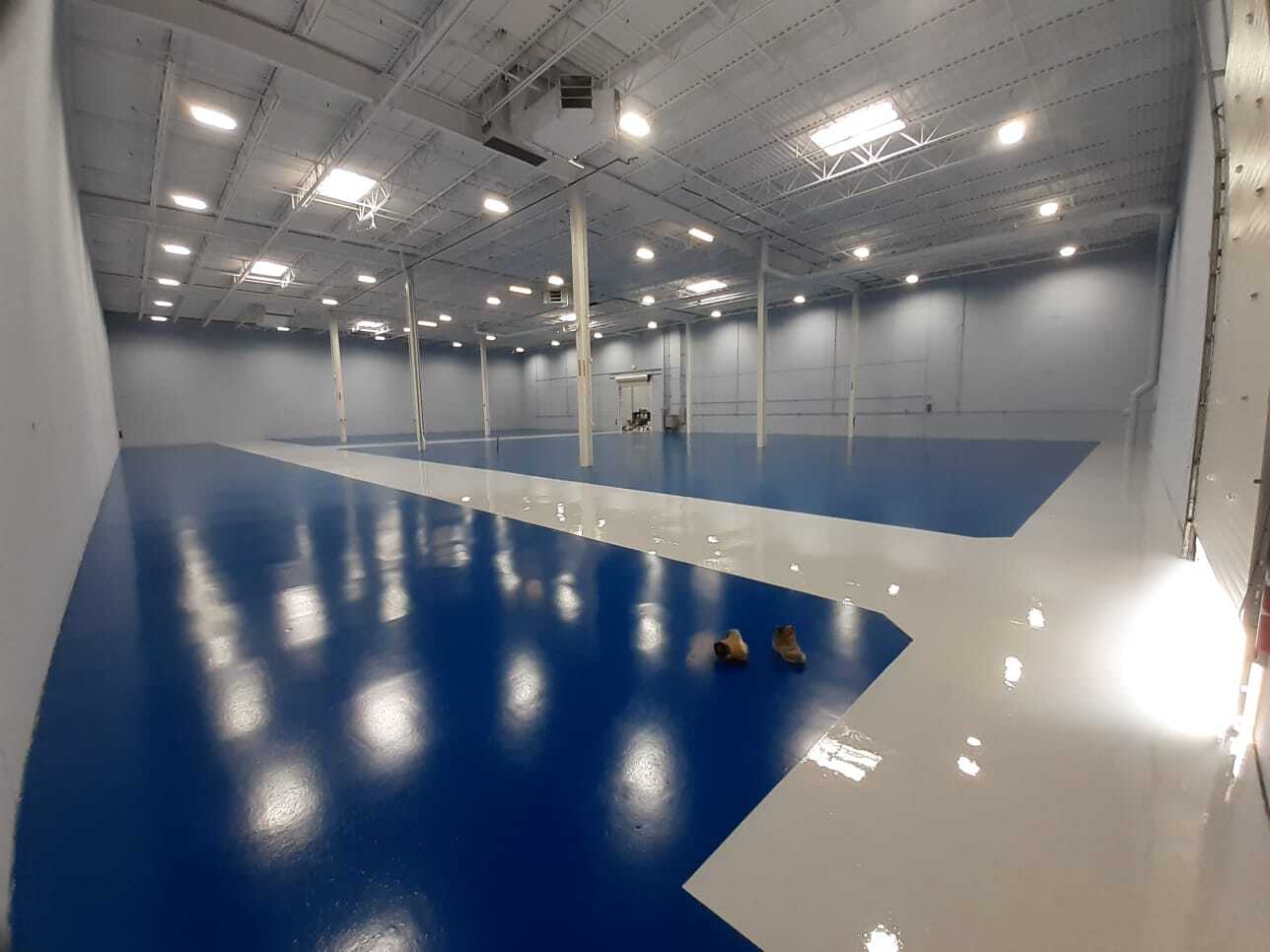
When you're running a food plant, pharmaceutical lab, or commercial kitchen, hygiene isn't optional—it's mission-critical. Contaminated surfaces can lead to product recalls, safety hazards, and costly downtime. And while walls and equipment get most of the attention, it's the floors that silently carry the biggest burden: foot traffic, spills, frequent cleanings, and constant exposure to bacteria.
At CustomCrete, we’ve worked with countless clients in sanitation-sensitive industries who needed flooring that could do more than just hold up under pressure—it had to actively support their safety standards. That’s where antibacterial urethane cement comes in.
In this blog, we’ll explain how urethane systems with antibacterial technology work, how they compare to other concrete flooring solutions, and why they’ve become a trusted option for facilities where cleanliness is non-negotiable.
What Is Urethane Cement Flooring?
Before diving into its antibacterial properties, it’s helpful to understand what urethane cement flooring is in general.
Urethane (also called polyurethane) is a resin-based floor coating known for its:
- Exceptional durability
- Resistance to chemicals, heat, and impact
- Long lifespan even under heavy use
It’s commonly used in industrial and commercial spaces because it holds up where traditional concrete alone would break down. It’s also flexible compared to epoxy, which allows it to better absorb impact and resist cracking.
There are several types of urethane coatings, including cementitious urethane, which combines urethane resin with cement, water, and other additives. This version is often used in places that need extreme durability and hygiene.
What Makes Urethane “Antibacterial”?
Antibacterial urethane contains additives—usually silver ion or other antimicrobial agents—that are mixed directly into the flooring material during manufacturing. These agents inhibit the growth of bacteria, mold, and other microbes on the floor’s surface.
Here’s how it works:
- Disruption of cell processes: Antimicrobial agents interfere with the basic functions of bacteria and fungi, preventing them from reproducing and spreading.
- Long-term integration: Because the additives are part of the floor's chemical makeup—not just applied as a surface treatment—they don’t wear off over time with cleaning or use.
- Around-the-clock protection: Antibacterial urethane cement provides ongoing protection, not just immediately after cleaning, making it a consistent line of defense in high-risk areas.
It’s important to note that antibacterial doesn’t mean sterile. These floors don’t eliminate all bacteria, but they do significantly reduce surface-level growth and microbial colonization—especially between cleaning cycles.
Why Facilities Choose Antibacterial Urethane Cement
When it comes to choosing a flooring system that supports both hygiene and durability, antibacterial urethane cement stands out for several compelling reasons.
1. Reduces Risk of Contamination
In spaces where food, medicine, or sensitive equipment is handled, a cleaner floor isn’t just nice—it’s mandatory. Urethane cement floors with antibacterial properties help minimize the risk of cross-contamination, especially in zones where spills or residue are common.
2. Supports Regulatory Compliance
Industries like healthcare and food processing are subject to strict health codes. Using antibacterial urethane cement can help businesses meet standards set by organizations like the FDA, USDA, or local health departments.
3. Works Well with Rigorous Cleaning
Because these floors are resistant to heat, chemicals, and water, they can withstand aggressive cleaning protocols like steam cleaning or acidic sanitizers—without degrading or losing their antimicrobial effect.
4. Lasts in Harsh Environments
Urethane is especially valued for its performance in extreme conditions, including:
- Constant moisture or washdowns
- Thermal shock from hot water or equipment
- Chemical exposure from disinfectants, solvents, or acids
This makes it a strong choice for breweries, meat-packing facilities, commercial kitchens, and hospital environments where flooring takes a daily beating.
How Is Antibacterial Urethane Cement Installed?
Installing antibacterial urethane cement is similar to other high-performance coating systems, but it requires professional surface prep and application to ensure effectiveness. The process typically includes:
- Concrete surface preparation – Grinding or shot blasting removes contaminants and roughs the surface for better adhesion.
- Priming (if needed) – Some applications require a primer layer depending on the substrate and product.
- Application of urethane coating – The antibacterial urethane cement is poured or rolled on and allowed to cure.
- Optional topcoat – In some cases, an additional wear layer or slip-resistant additive is added for extra durability.
When Should You Consider Antibacterial Urethane Cement?
If your facility experiences any of the following conditions, urethane cement flooring with antibacterial properties could be a smart fit:
- Frequent spills or moisture that require strict cleaning protocols
- Heavy foot traffic and rolling equipment that cause wear on traditional floors
- Strict sanitation requirements for food, beverage, healthcare, or pharmaceutical operations
- Concerns about mold or bacterial buildup in corners, seams, or hard-to-clean surfaces
How Does It Compare to Other Flooring Options?
Antibacterial urethane cement stands out among industrial flooring systems for its unique combination of hygiene, durability, and environmental tolerance. Here's how it stacks up compared to other common flooring options:
- Compared to epoxy: Both are highly durable, but epoxy is less resistant to thermal shock and moisture. In consistently wet or hot environments, epoxy can peel, bubble, or wear down more quickly. Unlike antibacterial urethane cement, epoxy does not include built-in antimicrobial properties unless added through separate coatings.
- Compared to vinyl: Some vinyl flooring products offer antimicrobial properties, but they often fall short on durability and heat resistance. Vinyl is more prone to tears, dents, and adhesive failure in heavy-use industrial settings, making it less ideal for areas with rolling equipment or frequent cleaning with harsh chemicals.
- Compared to polished concrete: While polished concrete provides a sleek, low-maintenance finish, it doesn’t offer antimicrobial protection. It’s also more vulnerable to moisture penetration and thermal stress. For facilities with strict hygiene standards, polished concrete may not offer enough protection or cleanliness benefits.
Final Thoughts
Whether you’re managing a food production facility, operating a commercial kitchen, or looking to upgrade a healthcare space, antibacterial urethane cement could be a solution that protects both your operations and your people.
If you're evaluating hygienic flooring options, knowing how urethane works—and where it performs best—can help you make a smarter, safer investment. For more information, read our next article, “What is Urethane Cement?”.
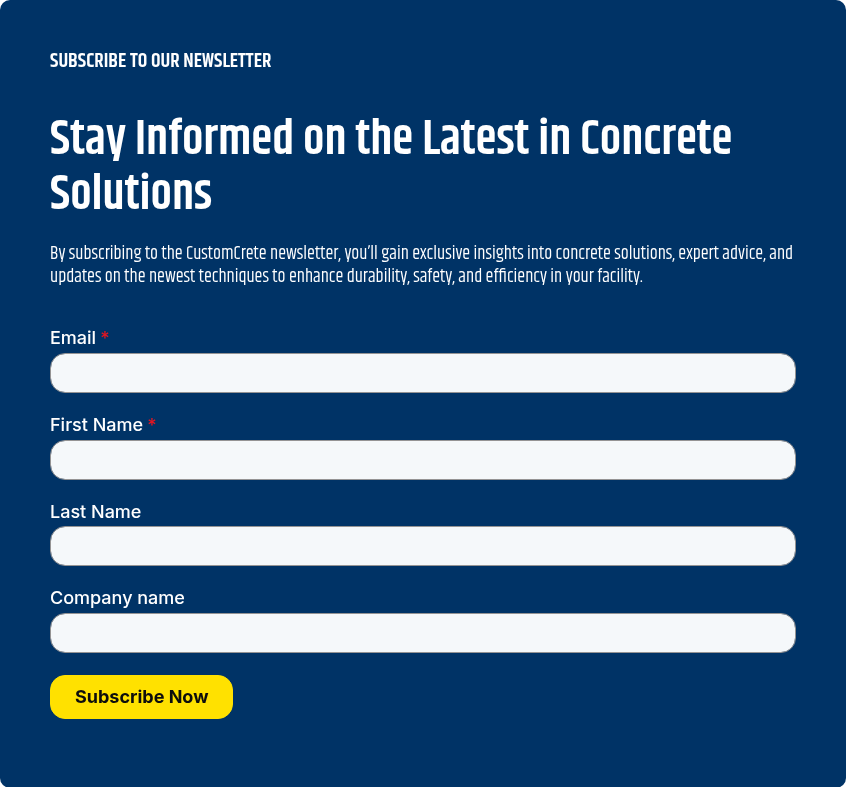
Topics: