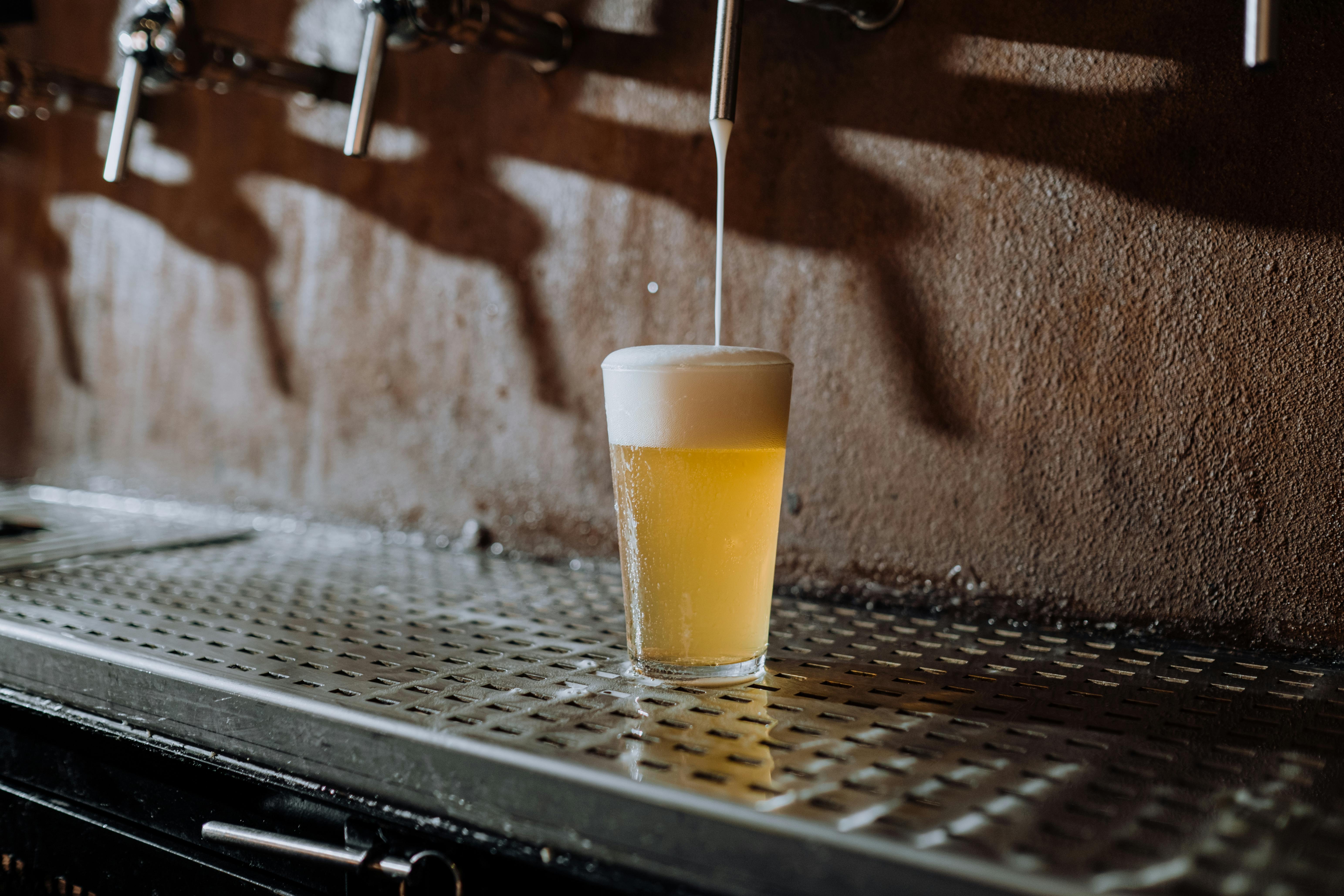
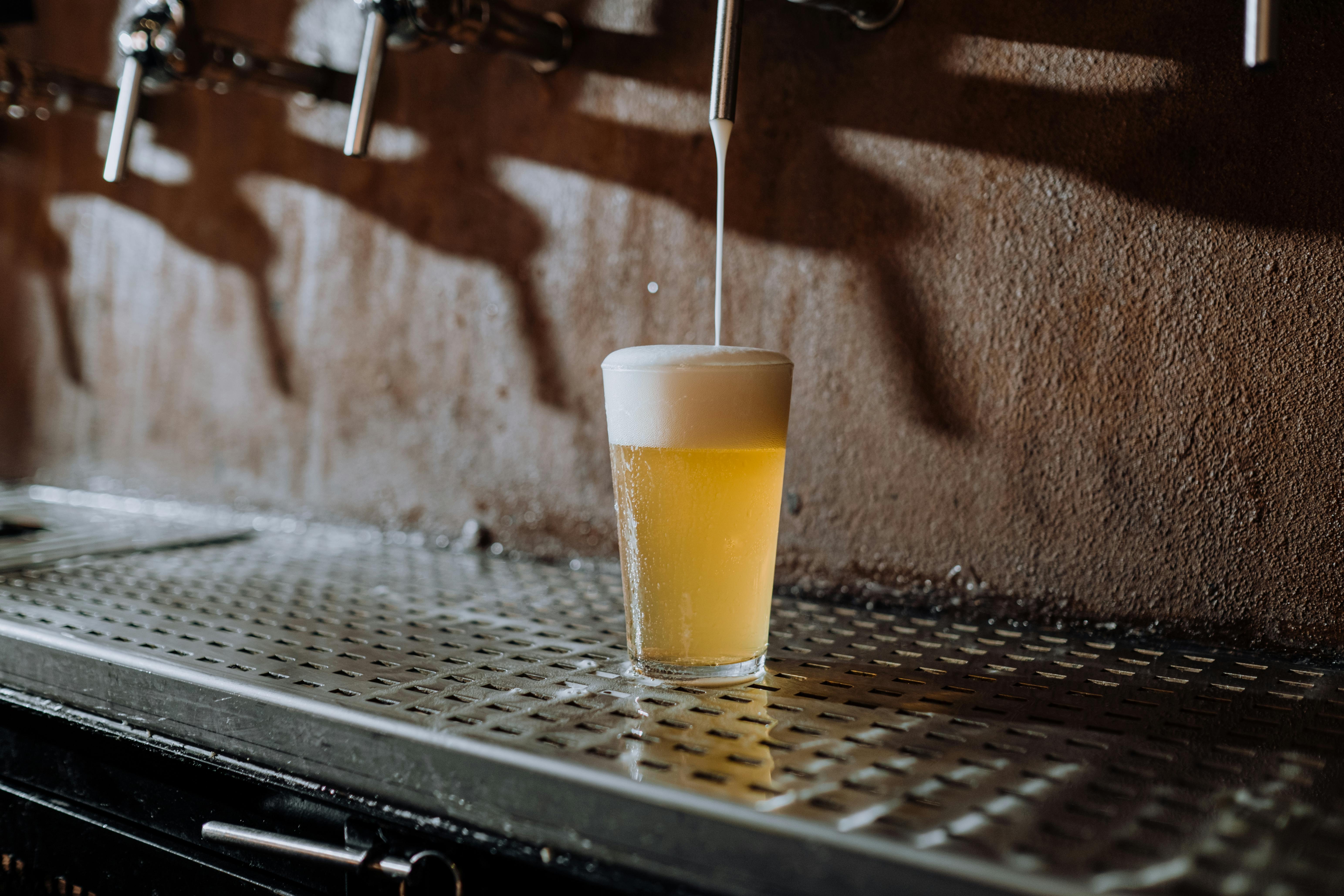
When designing or upgrading a brewery, it’s easy to focus on equipment, branding, or layout. But flooring? That’s often overlooked—until it causes problems. The truth is, brewery flooring plays a big role in both safety and aesthetics, especially when comparing the demands of a brewhouse to those of a taproom.
These two spaces serve very different purposes. One is a workhorse—the brewhouse. The other is the face of your brand—the taproom. And each needs a flooring solution that’s tailored to its function.
Let’s break down what matters most for each, and how to choose the best flooring for both parts of your brewery.
Your brewhouse is the beating heart of your operation. It’s where ingredients become beer. It’s also where the floors take a beating. From caustic chemicals and boiling water to heavy kegs and constant cleaning, the environment is harsh and wet—every single day.
So what should brewhouse flooring be able to handle?
Pro Tip: If you're building or renovating, plan early for floor prep, coatings, and drainage. Retrofitting later can be expensive and disruptive.
Now contrast that with your taproom—the public-facing space where customers drink, socialize, and experience your brand. The demands here are different. While spills and foot traffic still happen, the atmosphere is more controlled. Aesthetic plays a much bigger role.
Taproom flooring should still be durable—but it also needs to look the part.
Pro Tip: Use a matte or satin finish to avoid overly reflective floors, which can show every smudge or scratch.
It’s clear that brewery flooring isn’t one-size-fits-all. A single facility needs multiple performance profiles—one for heavy-duty brewing and another for customer-facing hospitality.
In the brewhouse, the flooring must prioritize performance and safety. These surfaces face frequent washdowns, exposure to chemicals, and constant foot and equipment traffic. Slip resistance is critical, and hygiene is a must. Materials like urethane cement or quartz-broadcast epoxy systems are common because they can handle moisture, thermal shock, and harsh cleaning agents without degrading.
In contrast, the taproom demands visual appeal and comfort. While it still needs to be easy to clean and slip-resistant—especially near the bar or entry—there’s more flexibility in design. Many taprooms opt for polished concrete, epoxy flake, or metallic epoxy, depending on their brand aesthetic.
Your brewery isn’t just a production site or a bar—it’s both. And each part deserves flooring that fits its specific job.
Choosing the right brewery flooring early on helps you avoid costly repairs, keeps your team and guests safe, and enhances your brand from the ground up. If you are interested in more information, read our next blog, “Why is Thermal Shock Important in Food and Beverage Facilities?”.