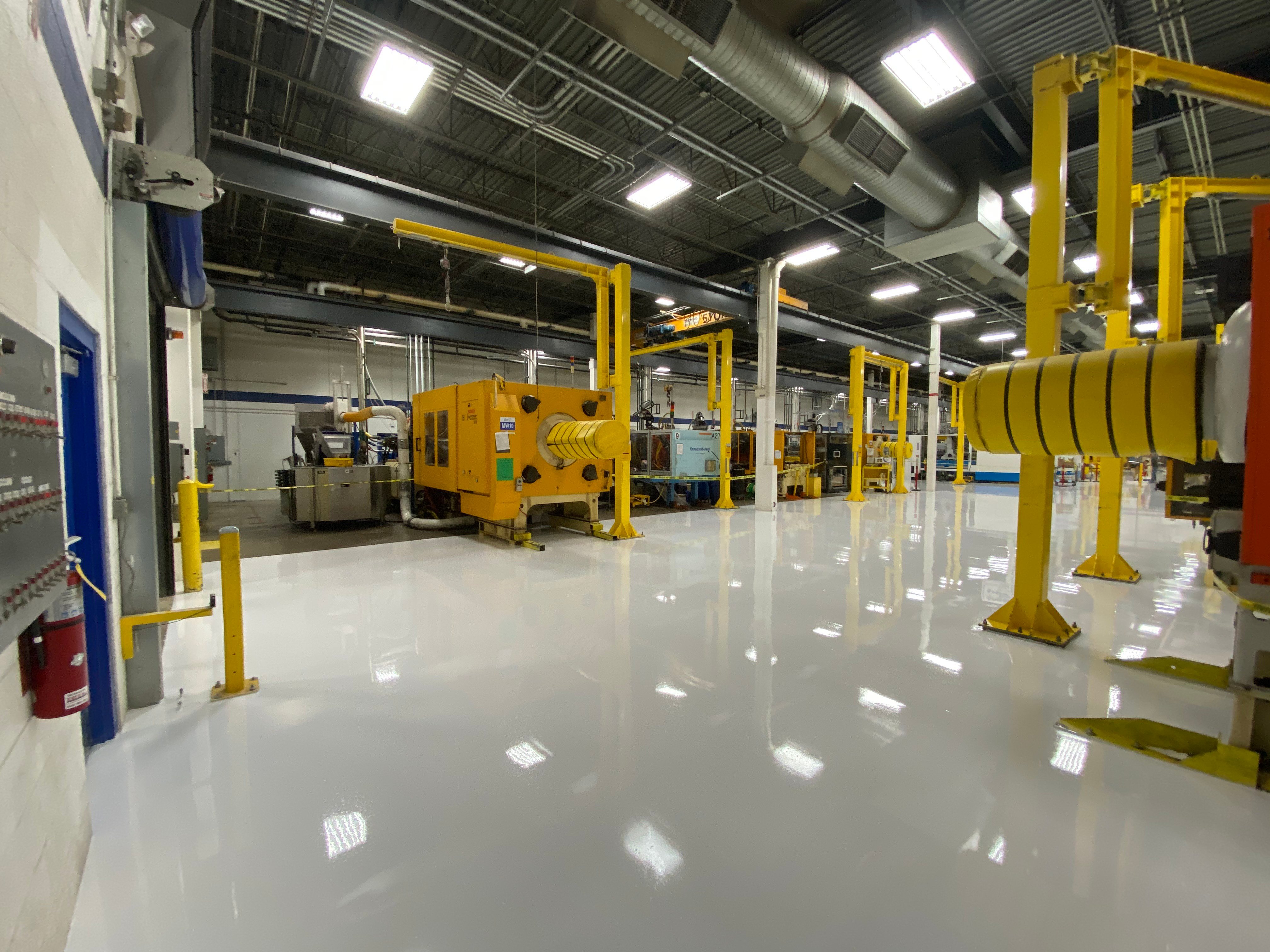
Topics:
Are you considering epoxy flooring for your commercial space but feeling uncertain about the cost? You’re not alone. For many businesses, the price of epoxy can seem difficult to navigate, especially when trying to balance quality and budget. It’s natural to ask: “How much will it really cost to install epoxy flooring, and what can I expect for my specific space?”
At CustomCrete, we've helped many businesses choose their floors. With 20 years of industry experience, we know how essential it is to provide clear, transparent pricing. That’s why we’re here to break down exactly what you can expect when it comes to the cost of epoxy flooring, so you can confidently move forward with a solution that fits your needs.
This article will guide you through a standard two-coat epoxy flooring job. We will focus on the basic epoxy coating, the most common type used in commercial settings. We’ll provide a detailed pricing breakdown based on both per square foot and for a standard 5,000-square-foot area, so you can plan your investment wisely. Let’s dive in.
When you’re looking to invest in epoxy flooring, the type of system you choose will significantly impact the overall cost. We'll break down the price ranges for a standard two-coat epoxy coating. (Two-coat for the initial coating and then the top-coat) This will show you what to expect to pay based on your project's size and complexity.
Standard epoxy coatings are the best for commercial spaces, like warehouses and factories. These coatings provide a strong, durable finish. It resists wear, chemicals, and moisture. It's ideal for high-traffic areas and places with heavy equipment. This option is budget-friendly and offers excellent value for large spaces needing a long-lasting solution.
Epoxy coatings provide exceptional durability for high-traffic commercial environments. When applying standard epoxy, minimal surface prep may be required if your concrete is in good condition. This keeps costs relatively low and makes this option an affordable choice for businesses looking for durable flooring without breaking the bank.
Epoxy can withstand extreme conditions. These include high foot traffic, chemical spills, and heavy machinery. This is what makes it an ideal choice for industrial settings, factories, and warehouses. It’s a low-maintenance, easy-to-clean surface. It can greatly extend your floors' lifespan. It is a smart, cost-effective solution for business owners. They want a high-performance floor that doesn't need constant upkeep.
While the price ranges above give you a solid estimate, there are several factors that will influence the final cost of your epoxy flooring project. Here’s a breakdown of the key elements that could affect your pricing:
Larger projects often cost less per square foot. They benefit from bulk material discounts and more efficient labor. Our crew can work continuously without frequent stops or moving equipment, reducing the overall cost. Smaller projects, however, may require more precision and time, especially in tight spaces, leading to a higher price per square foot.
To illustrate this point further, imagine a vast, open warehouse floor compared to a small, cluttered retail space. This example warehouse allows for long, uninterrupted passes with our equipment, maximizing efficiency. The retail space requires constant maneuvering around displays and fixtures. This slows down the process and increases labor time.
The condition of your existing concrete slab significantly impacts the cost. If your floor has imperfections like cracks or remnants of old coatings (epoxy, glue, etc.), diamond grinding will be necessary to prepare the surface. The more preparation required, the higher the cost.
Think of it like preparing a wall for painting. A smooth, new wall requires minimal preparation, while a damaged wall with peeling paint demands extensive patching and sanding before the first coat can be applied. Similarly, the condition of your concrete floor directly affects the amount of preparation needed, influencing the overall project cost.
Projects that involve complex layouts, such as those with obstacles, fixtures, or tight corners, can lead to higher costs. Our equipment is large. It needs careful maneuvering in these spaces. This makes it harder to seal areas that aren't open and clear. For instance, a wide-open warehouse floor is generally less expensive to seal than a smaller space filled with various obstructions.
A good example is a manufacturing facility with large machinery bolted to the floor. In these cases, our team needs to work around the equipment with precision, sometimes using specialized tools to handle the challenges. This added level of difficulty contributes to the overall cost of the project.
Easy access to your space is crucial. If your project is in a high-rise with limited elevator access, it will take more time and effort to move our equipment. This will increase labor costs. Things that make the facility easier to enter and exit like a loading dock, freight elevator, or even a simple ramp will make the process more efficient and potentially reduce costs.
Consider the challenges of moving heavy equipment to a high floor of an office building with small elevators. The time spent navigating these limitations translates to increased labor costs. A ground-level facility with a loading dock allows for quick access. This streamlines the process and may cut costs.
You want the best but it’s hard to know where to start. At CustomCrete, we believe in empowering you to make informed decisions. We’ll guide you through the options and help you choose the best sealing solution for your specific needs and budget.
If you’re ready to get a precise quote for your project, the next step is simple: Contact us for a quote. We’ll walk you through the options and make sure you get exactly what you need, without any surprises.
Topics: