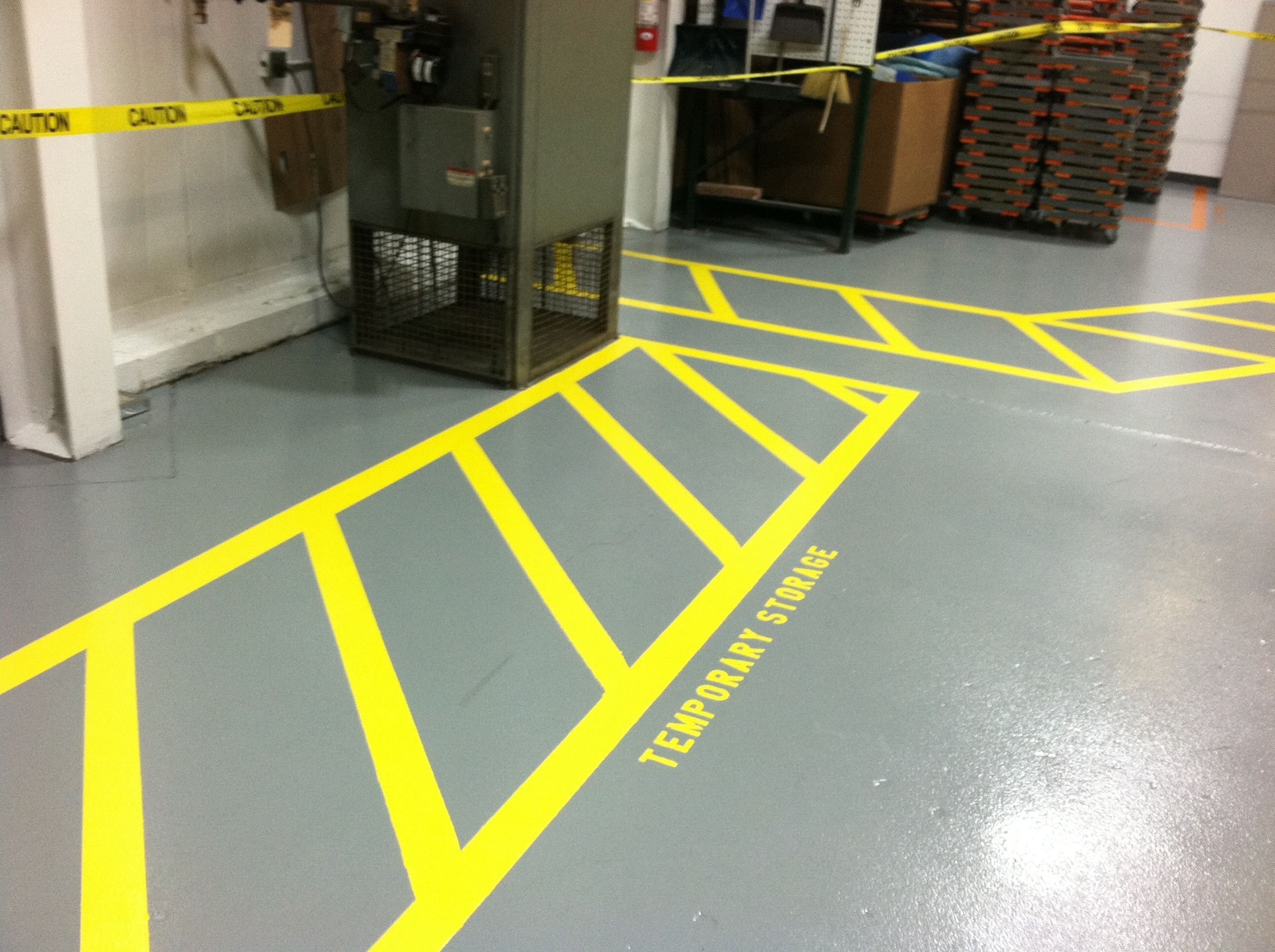
Topics:
July 17th, 2025
3 min read
By Tom Dassie
In busy industrial and commercial facilities, safety and organization can easily become overlooked amid daily operations. But one of the simplest, most cost-effective ways to improve both is by using color-coded line striping. Whether you manage a warehouse, manufacturing plant, or distribution center, clearly marked walkways and zones can dramatically reduce the risk of accidents and improve productivity.
In this blog, we’ll explore the purpose behind line striping, how color coding contributes to safer environments, and the best practices for implementing a durable, effective striping system in your facility.
Line striping isn’t just about looks—it’s about safety and clarity. In facilities with forklifts, pallet jacks, pedestrian traffic, and storage areas all operating side-by-side, a clearly defined layout reduces confusion and accidents.
Facilities without striping are often harder to navigate, leading to:
A strategic line striping plan gives everyone—from employees to visitors—a better understanding of where to walk, where to work, and what to avoid.
Color-coded line striping enhances the clarity of your space and supports compliance with industry standards like OSHA and ANSI. While there’s no universally enforced color code, many facilities follow these commonly accepted practices:
By assigning consistent meanings to colors, your facility creates an intuitive visual language that makes navigation faster and safer.
The most effective use of line striping depends on your layout and how traffic flows throughout your facility. Here are a few key areas where striping can add value:
Clear walkways separate foot traffic from moving vehicles, especially in loading docks and warehouses. Striping ensures employees know where to walk and stay visible to forklift drivers.
Designating specific lanes for machinery reduces the risk of collision and damage. Striped paths help operators stay within safe zones and avoid blind spots or congested areas.
Labeling pallet and rack locations with striping keeps materials organized and prevents overflow into walkways or traffic lanes.
Areas around machinery, electrical panels, or overhead hazards should be striped to warn of potential danger and maintain required clearance zones.
For striping to be effective, it needs to last. In industrial environments with heavy equipment, moisture, or temperature swings, painted stripes alone may not hold up.
Options for more durable striping include:
It’s important to match your line striping material to your floor type and daily traffic to ensure long-term visibility and performance.
A few smart strategies can help you get the most from your investment in striping:
Many facilities refresh their striping during regular floor maintenance or when applying a new coating system to ensure consistency and visibility.
While safety is the most immediate benefit, line striping also improves:
These gains can translate into real savings—reduced downtime, fewer accidents, and better use of labor and materials.
Color-coded line striping may seem like a small detail, but it plays a big role in shaping how people move, work, and stay safe in your facility. By investing in clear, durable markings, you support a workplace that’s not only safer—but also more productive and easier to manage.
Whether you’re reconfiguring your layout or simply want to upgrade your current markings, a professional line striping system is one of the most efficient ways to make a lasting impact.
If you would like to learn more about CustomCrete’s line striping solutions, visit our Line Striping service page.
Topics: